9. Цилиндро — поршневая группа
Цилиндры (рис. 18) рассматриваемых автотракторных двигателей съемные. Отдельно изготовленный цилиндр называют гильзой. Применение вставных гильз позволяет увеличить срок службы блок-картера за счет замены изношенных гильз новыми. Гильза цилиндра изготовлена из легированного чугуна. Внутренняя поверхность гильзы, называемая зеркалом, тщательно обработана и закалена. По внутреннему диаметру гильзы сортируют на три размерные группы: Б, С и М (большая, средняя и малая).
Обозначения размерной группы наносят на торце буртика 1 гильзы.
Рис. 18(12). Конструкции цилиндров: а — «мокрая» гильза цилиндра, б — схема установки гильзы двигателя, в — цилиндр с воздушным охлаждением, 1 — буртик, 2 — верхний поясок, 3 — нижний поясок, 4 — резиновое уплотнительное кольцо, 5 — гильза цилиндра, 6 — вставка, 7 — водяная рубашка, 8 — уплотнительная прокладка, 9 — картер
Гильзы, наружная поверхность которых омывается охлаждающей жидкостью называются «мокрыми» (рис. 18, а). На наружной поверхности гильзы выполнены два посадочных пояска 2 и 3, которые служат для плотной установки гильзы в блоке. Между нижним пояском гильзы и блоком цилиндра монтируют резиновые уплотнительные кольца 4, предотвращающие протекание воды в картер из водяной рубашки блока. У одних двигателей резиновые кольца устанавливают в выточки, выполненные на нижнем пояске гильзы, а у других — в расточке блока. Верхний торец гильзы выступает над плоскостью блока, что обеспечивает лучшее обжатие металлоасбестовой прокладки и создает надежное уплотнение от прорыва газов из цилиндра. Износ верхней части гильз уменьшается при установке в некоторых автомобильных двигателях износостойких вставок 7 (рис. 18, б) из антикоррозийного чугуна. В некоторых двигателях между основанием нижнего выступа блок-картера и опорной поверхностью нижнего буртика устанавливают медную кольцевую прокладку 8.
Цилиндры двигателей с воздушным охлаждением (рис. 18, г) снабжены снаружи охлаждающими ребрами. В нижней части цилиндра имеется бурт, который упирается в поверхность картера. Между картером и буртом устанавливают медное кольцо. Каждый цилиндр вместе с головкой закрепляют специальными (анкерными) шпильками на картере.
Поршни (рис. 19) воспринимают и передают шатуну усилия, возникающие
от давления газов, а также обеспечивают протекание всех тактов рабочего цикла. Они подвергаются действию высоких температур и давлений и движутся со значительными скоростями внутри цилиндра. В соответствии с условиями работы материал поршня должен обладать высокими механическими свойствами и износостойкостью, быть легким, хорошо отводить тепло. Поэтому в современных двигателях поршни отливают из легкого, но достаточно прочного алюминиевого сплава.
Рис. 19(13). Конструкция поршня: а — поршень дизельного двигателя, б — сечения поршней дизельных двигателей, в — поршень карбюраторного двигателя, г — поршневой палец, 1 — маслосбрасывающая кромка, 2 — канавка для маслосъемного кольца, 3 — канавка для стопорного кольца, 4 — отверстие для подвода масла к поршневому пальцу, 5 — канавки для компрессионных колец, 6 — камера сгорания в поршне, 7 — прорезь, 8 — стопорное кольцо поршневого пальца; А — днище, Б — головка, В — направляющая часть, Г — бобышки, Д — холодильник, Е — места клеймения массы и размерной группы поршня, Ж — метка направления установки поршня, З — место клеймения размерной группы поршневого пальца
Поршень (рис. 19, а) имеет вид перевернутого стакана. Он состоит из днища А, головки Б (или уплотняющей части) и направляющей части В, называемой юбкой. Днище поршня дизельного двигателя делают фасонной формы с выемкой, которая зависит от способа смесеобразования и расположения клапанов и форсунок. Такая форма днища способствует лучшему перемешиванию воздуха с поступающим в цилиндр топливом и более полному его сгоранию.
На внешней поверхности головки и юбке проточены канавки 5 и 2 для компрессионных и маслосъемных колец. Число колец, устанавливаемых на поршне, зависит от типа двигателя и частоты вращения коленчатого вала. Для повышения износостойкости у некоторых двигателей в канавку под верхнее компрессионное кольцо заливают стальную вставку, что увеличивает долговечность сопряжения кольца с канавкой. По окружности канавок под маслосъемные кольца просверлены сквозные отверстия для отвода масла в картер двигателя.
На внутренней стороне юбки имеются два прилива — бобышки Г, в отверстия которых устанавливают поршневой палец. Бобышки соединяются ребрами с днищем, увеличивая прочность поршня. В бобышках проточены кольцевые канавки 3 для стопорных колец. На наружной поверхности поршня против бобышек сделаны срезы — «холодильники», где скапливается масло, способствующее охлаждению утолщенной части поршня и предохраняющее поршень от заклинивания. С этой же целью применяют поршни, у которых диаметр юбки больше диаметра головки, а юбка имеет овальное сечение (большая ось овала перпендикулярна оси поршневого пальца).
По величине наружного диаметра юбки поршня, как и цилиндры, сортируют на три размерные группы: Б, С и М. Обозначение размерной группы наносят на днище поршня. При сборке группа поршня должна быть одинаковой с группой гильзы.
Поршни сортируют на две размерные группы по диаметру отверстия под
поршневой палец и маркируют краской (черной или желтой) на бобышках поршня.
На головке поршня некоторых тракторных двигателей сделаны мелкие кольцевые канавки глубиной 0,3 мм (рис.19, б). В них задерживаются продукты сгорания масла (нагар), что предотвращает преждевременное закоксовывание поршневых колец.
В карбюраторных двигателях применяют поршни с плоским днищем (рис.19, в), получившие широкое распространение из-за простоты изготовления и меньшего нагрева при работе. У некоторых автомобильных двигателей часть юбки под бобышками удалена для прохода противовесов коленчатого вала при нижнем положении поршня и его облегчения. Поршни имеют поперечные прорези 7 под головкой, на юбке может быть выполнен продольный или Т-образный разрез. Прорези повышают упругость юбки поршня, что устраняет опасность заклинивания. Если на юбке поршней имеются прорези, то их устанавливают в двигатели так, чтобы боковое давление при рабочем ходе испытывала часть поршня без разреза. Правильной установке поршня по направлению в двигателе помогает надпись, выполненная на юбке.
Поршневые пальцы (рис.19, г) изготовлены пустотелыми из стали. От осевого перемещения палец удерживается разжимными стопорными кольцами 8, которые установлены в канавках бобышек поршня. Палец соединяет поршень с шатуном. В отверстие втулки верхней головки шатуна палец вставляют с зазором, а в поршень — с натягом. Во время работы двигателя из-за различных коэффициентов линейного расширения материалов между поршнем и пальцем при достижении рабочей температуры появляется зазор, и палец имеет возможность поворачиваться в бобышках поршня. Такой палец называют плавающим.
По величине наружного диаметра пальцы разделяют на две размерные группы. Размерные группы маркируют, как и отверстия в бобышках поршня,
черным и желтым цветом. Краску наносят на внутреннюю поверхность пальца 8. При сборке пальца с поршнем необходимо помнить, что их размерные группы должны быть одинаковы.
Поршневые кольца (рис.20) создают плотное, подвижное соединение между поршнем и цилиндром. По назначению их разделяют на компрессионные 1 и маслосъемные 2. Компрессионные кольца предотвращают прорыв газов из камеры сгорания в картер. Маслосъемные кольца препятствуют проникновению масла из картера в камеру сгорания, снимая излишки масла со стенки цилиндра.
Кольца изготовляют из легированного чугуна или стали. Наружный диаметр кольца в свободном состоянии больше внутреннего диаметра цилиндра. Часть кольца вырезана, вследствие чего при установке в цилиндр кольцо пружинит и хорошо прилегает к его поверхности. Вырез в поршневом кольце называют замком. Замки поршневых колец могут быть косые или прямые. Наибольшее распространение получило кольцо с прямым замком, как более простое и дешевое в изготовлении. С целью уменьшения утечки газов через зазоры в замках кольца устанавливают замками в разные стороны, желательно на равном расстоянии по окружности. Для уплотнения, обеспечивающего герметичность цилиндра, у карбюраторных двигателей на поршни размещают 2—3, а у дизелей, где давление газов в цилиндрах более высокое, 3—4 компрессионных кольца. В канавках поршня кольца устанавливают с небольшим зазором и они могут свободно перемещаться относительно поршня. Если поршневые кольца неплотно прилегают к стенке цилиндра, то газы, прорываясь через просветы между цилиндром и кольцом, вызывают перегрев кольца. При этом образующиеся шлаковые отложения заполняют зазоры между кольцами и стенками канавок поршня по высоте.
Рис. 20(14). Поршневые кольца: а — внешний вид, б — формы компрессионных колец в рабочем состоянии, в — составное маслосъемное кольцо, г — расположение колец на поршне; 1 — компрессионное кольцо, 2 — маслосъемное кольцо, 3 — плоские стальные кольца, 4 — осевой расширитель, 5 — радиальный расширитель, 6 — поршень
Кольца перестают свободно перемещаться и пружинить. Это явление носит название пригорания (закоксовывания) колец и сопровождается потерей мощности двигателя и повышенным расходом масла.
В поперечном сечении компрессионные кольца имеют различную форму (рис. 20, б). По сравнению с кольцом прямоугольного сечения кольцо с конической наружной поверхностью имеет меньшую опорную поверхность, что обеспечивает его быструю приработку и хороший контакт с цилиндром по всей окружности. Компрессионные кольца некоторых двигателей имеют по внутреннему диаметру сверху кольца фаску или выточку. При установке в цилиндр такие кольца деформируются (скручиваются) и прилегают к зеркалу цилиндра нижней кромкой. Поэтому скручивающиеся кольца работают подобно конусным и в то же время имеют меньшее перемещение по поршню в вертикальном направлении. Форма кольца с поперечником в виде односторонней трапеции уменьшает возможность зависания в канавках поршня при больших отложениях нагара и улучшает его прилегание к стенке цилиндра.
Трущаяся о цилиндр поверхность верхнего компрессионного кольца хромируется с целью увеличения срока службы всех колец и цилиндра. Трущаяся поверхность поршневых колец многих двигателей облуживается для улучшения их приработки.
Маслосъемные кольца (одно или два) устанавливают ниже компрессионных колец. Они в отличие от компрессионных колец имеют сквозные прорези или состоят из двух колец скребкового типа. На поршни некоторых двигателей устанавливают составные маслосъемные кольца (рис. 20, в) изготовленные из двух стальных дисков и двух гофрированных расширителей — осевого и радиального. Осевой расширитель, расположенный между дисками, плотно прижимает их к стенкам канавки поршня. Радиальный расширитель плотно прижимает диски к зеркалу цилиндра.
Сборные кольца хорошо прилегают к поверхности цилиндра и обеспечивают низкий расход картерного масла.
studfiles.net
Что такое ЦПГ?
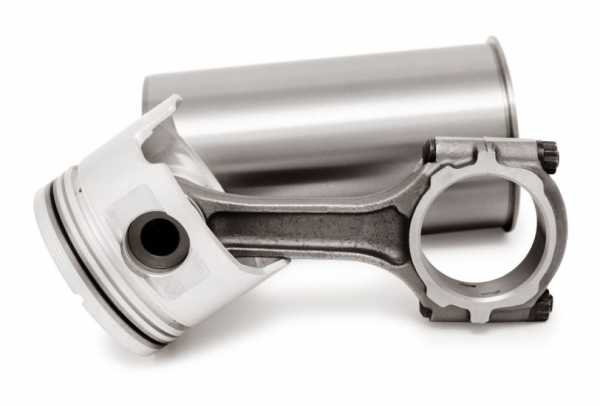
Цилиндропоршневая группа двигателя внутреннего сгорания (ЦПГ) — поршень с компрессионными и маслосъемными кольцами, которые называются поршневыми кольцами, а также гильза цилиндра. Кольца установлены в специальные канавки на поршне. Именно поршневые кольца вступают в контакт с рабочей поверхностью цилиндра, а точнее с гильзой.
В процессе работы двигателя поршень с установленными кольцами совершает возвратно-поступательные движения внутри гильзы, в результате чего рабочая поверхность гильзы (зеркало цилиндра) подвергается постепенному износу. Также износу подвержены и сами компрессионные и маслосъемные кольца.
От состояния цилиндро-поршневой группы напрямую зависят важнейшие показатели, необходимые для стабильной работы двигателя внутреннего сгорания. Состояние ЦПГ влияет на показатель компрессии (давления) в цилиндрах ДВС. Необходимая компрессия бензинового и дизельного мотора обеспечивает уверенный холодный и горячий запуск двигателя, его мощность, экологичность и другие эксплуатационные показатели.От исправности и состояния ЦПГ также зависит расход топлива и моторного масла, а также продолжительность срока службы двигателя до его капитального ремонта. Ремонт цилиндро-поршневой группы двигателя подразумевает замену маслосъемных и компрессионных колец, расточку блока цилиндров, установку новых поршней и шатунов, гильзовку блока цилиндров.
Читайте также
krutimotor.ru
КОНСТРУКЦИИ ЦИЛИНДРОПОРШНЕВОЙ ГРУППЫ И МЕХАНИЗМА ГАЗОРАСПРЕДЕЛЕНИЯ
Цилиндропоршневая группа ДВС, конструктивно являясь составной и неотъемлемой частью кривошипно-шатунного механизма, формирует рабочий объем двигателя, обеспечивает протекание внутрицилиндровых процессов и, в частности, преобразует энергию рабочего тела в механическую работу за счет движения поршня. Цилиндропоршневая группа состоит из цилиндровой гильзы (цилиндра), поршня, компрессионных и маслосъемных колец, поршневого пальца и его стопоров. Поскольку о конструкции цилиндра и гильзы цилиндра говорилось ранее, при описании остова двигателя, рассмотрим оставшиеся детали и начнем с поршня.
Поршень, рис. 8.1, является подвижной частью стенки цилиндра, его верхняя поверхность – огневое днище – формирует камеру сгорания двигателя. Являясь подвижным элементом, поршень должен обеспечивать, во-первых, уплотнение цилиндра и, во-вторых, компенсировать действие нормальной силы – реакцию опоры на зеркало цилиндра. Поэтому функционально поршень состоит из верхней части – днища или головки поршня, на которой размещаются лабиринтное уплотнение в виде поршневых колец и из нижней – тронка или юбки, которая является направляющей и воспринимает действие нормальной силы.
Рис. 8.1. Поршень современного дизельного двигателя
Поршень современного двигателя изготавливается, в основном из алюминиевых сплавов с большим содержанием кремния типа АЛ – 25. Заготовки поршней изготавливаются методом литья под давлением или жидкой штамповки, которая обеспечивает требуемую прочность, а материал, обладая низким коэффициентом термического расширения, позволяет задавать минимальные зазоры между тронком поршня и гильзой. На малоразмерных ВОД поршни делаются цельными, когда верхняя часть поршня, на которой располагаются поршневые кольца и нижняя часть изготовлены из единой заготовки. Для крупных высокофорсированных дизелей в силу большой теплонапряженности деталей, поршни делают составными, в которых верхняя часть изготавливается из жаропрочных сталей, способных выдерживать высокие температуры камеры сгорания. Хорошим литейным материалом для изготовления поршней является чугун, который, обладая высокими прочностными характеристиками, обеспечивает достойные антифрикционные свойства в паре трения поршень – гильза.
В малоразмерных двигателях умеренной форсировки теплоотвод от поршня, равно как и его смазка, происходит за счет масляного тумана, образующегося от стекающего и разбрызгиваемого из подшипников коленвала масла. Для улучшения теплосъема с поршней в форсированных дизелях с диаметром цилиндра более 100 мм используется принудительное охлаждение днища. Для этого в основной масляной магистрали устанавливаются масляные форсунки, которые подают масло на внутреннюю часть днища поршня. Возможна конструкция, когда масло на смазку – охлаждение поршней подается импульсами в определенные моменты через сопловое отверстие в нижней головке шатуна в момент совмещение отверстия масляного канала шатунной шейки с сопловым отверстием. В тех конструкциях высокофорсированных двигателей, когда вышеизложенные способы охлаждения оказываются не эффективными, используется барботажное охлаждение поршня. В днище поршня организуется внутренний кольцевой канал – масляная галерея – он может быть сформирован проточками в деталях составного поршня, а может быть отформован в отливке для цельного поршня. В масляную галерею масло может подаваться как через уже упомянутые форсунки, так и через верхнюю головку шатуна посредством специальной шарнирной конструкции. Канал масляной галереи снабжен отверстиями для стока подаваемого масла, причем слив организован так, что канал никогда не заполняется полностью, что собственно и обеспечивает интенсификацию теплоотвода за счет взбалтывания масла под действием знакопеременных сил инерции КШМ.
Поскольку поршень, как отмечалось ранее, является подвижной стенкой камеры сгорания, то огневое днище поршня имеет вид специальной лекальной формы, в соответствии с требуемой формой камеры сгорания для реализуемого в данном двигателе способе смесеобразования и сгорания. Кроме того, на поверхности огневого днища могут изготавливаться выемки под клапана механизма газораспределения, а также специальные глухие отверстия (возможно и резьбовые), необходимые для демонтажа поршня из цилиндра двигателя при проведении ремонтных мероприятий.
На боковой поверхности цилиндра верхней части поршня протачивают канавки под поршневые кольца. Форма канавок и их количество определено конструктором в зависимости от количества и формы колец.
Тронк поршня изготавливают с диаметром несколько большим, нежели диаметр места установки поршневых колец, при этом тронк поршня делается по копиру и имеет овально-бочкообразную форму. Такая сложная геометрия поршня предопределяется тепловыми деформациями поршня при достижении рабочих параметров двигателя. Так как теплоотвод в поршне происходит от огневого днища, то нижняя часть тронка имеет температуру более низкую, чем температура в зоне под поршневыми кольцами, т.е. имеет наименьшее тепловое расширение, а, следовательно, наибольший диаметр. Таким образом, определяется бочкообразность образующей поршня. В отливке поршня предусматриваются места для расточки посадки поршневого пальца (бобышки), и в этом месте поршень имеет утолщение. Неравномерность распределения материала, естественно провоцирует искажение геометрии детали при ее нагреве, поэтому места, где располагаются бобышки в поршне, занижают относительно основного диаметра тронка. Таким образом, определяется овальная форма тронка. В некоторых конструкциях высокофорсированных ВОД в отливку вводят специальные армирующие вставки из сплава, обладающего очень низким коэффициентом термического расширения (инваровые вставки). Эти вставки размещают в зоне перехода головки поршня в тронк около бобышек. Такая конструкция поршня позволяет минимизировать деформацию поршня от неравномерного нагрева в процессе работы двигателя. Кроме того, в подавляющем большинстве конструкций цельного поршня заливается кольцевая вставка из высоколегированного чугуна в месте проточки канавки под первое компрессионное кольцо, поскольку это место является самым тяжелонагруженным и изнашиваемым, ввиду специфики работы компрессионных колец, о которой разговор пойдет далее.
Расточка отверстия под поршневой палец в бобышках поршня производится с высокой точностью по переходной посадке или с небольшим зазором (порядка 0.02 мм) поэтому для установки поршневого пальца в расточку бобышек требуется нагрев поршня, обычно до температуры 80…120 оС, для появления зазора в соединении. При нагреве поршня в процессе работы в соединении поршень-палец появляется зазор, и палец обретает подвижность, такая конструкция узла называется с плавающим пальцем, альтернативой которой является уже упомянутая ранее конструкция с прессованным в шатун пальцем, в которой в сопряжении поршня с пальцем делается гарантированный зазор. Не смотря на простоту конструкции узла с прессованным пальцем, на дизелях она применима чрезвычайно редко ввиду одностороннего неравномерного износа пальца и, как следствие, малого ресурса в условиях дизельного двигателя. В конструкции узла с плавающим пальцем предусматривается ограничение осевого перемещения пальца в расточке бобышек. Для этого делаются проточки под установку стопорных колец или в отверстие бобышек устанавливаются заглушки.
Поверхность контакта тронка с зеркалом цилиндра имеет специальную обработку, обеспечивающую быструю и безаварийную прирабатываемость поршня. Это может быть гальваническое покрытие, напыление покрытия на основе графита и дисульфида молибдена, обработка, имеющая специальный микропрофиль и т.д.
Конструкция поршня крейцкопфного двигателя отлична от поршня тронкового двигателя. В связи с тем, что поршень крейцкопфного двигателя не воспринимает действие нормальной силы реакции опоры на цилиндр (эту силу воспринимает отдельный механизм), конструкция такого поршня не предусматривает наличие тронка. В этом случае поршень представляет собой оправку для установки поршневых колец, соединенную жестким штоком с башмаком крейцкопфного механизма.
Для уплотнения цилиндра поршневого ДВС используется лабиринтное уплотнение, состоящее из набора компрессионных колец, устанавливаемых в проточки верхней части поршня. Для обеспечения съема масла с поверхности зеркала цилиндра и для уменьшения количества масла, проникающего в камеру сгорания, определяющего расход масла на угар, за компрессионными кольцами устанавливаются маслосъемные кольца.
Количество поршневых колец определяется конструкцией ЦПГ и может составлять от 2 компрессионных и 1 маслосъемного кольца и более в различных комбинациях. При своей кажущейся простоте, конструкция кольца чрезвычайно сложна. Для обеспечения возможности монтажа, кольца изготавливаются разрезными со стыком. Компрессионное кольцо изготавливают таким образом, чтобы оно обладало собственной жесткостью, благодаря чему кольцо оказывает давление на стенку цилиндра, чем обеспечивает в статике полное прилегание торцевой поверхности к поверхности зеркала цилиндра и, следовательно, обеспечивало уплотнение цилиндра. При этом эпюра сил, действующих на зеркало цилиндра, за счет специальной эпюрной обработки (этот эффект может быть достигнут за счет термообработки – термофиксации) намеренно создается не равномерной, а имеющей максимумы у стыка кольца. При нормальной работе кольца, давление газов, развиваемое в цилиндре, передается на кольцо и формирует эпюру действия газовых сил. Давление газа действует на кольцо со стороны камеры сгорания и, во-первых, прижимает его с силой, эквивалентной разности давления над и под кольцом, к поршневой канавке, чем собственно и обеспечивается уплотнение лабиринта. Во-вторых, в связи с тем, что радиальная толщина кольца всегда меньше глубины канавки в поршне, давление газа оказывает воздействие на внутреннюю поверхность кольца, которое за счет этого дополнительно прижимается к зеркалу цилиндра. Очевидно, что сила собственной упругости кольца суммируется с действием газовых сил. При этом эпюра действия газовых сил оказывается неравномерной, с минимумами в стыке, поскольку через зазор в стыке кольца происходит утечка газа. Зазор в стыке называют тепловым зазором, он позволяет кольцу удлиняться при нагреве и обеспечивает постоянную подвижность кольца и безаварийную работу уплотнения. Теперь становится понятной причина, по которой статическая эпюра сил собственной жесткости кольца изготавливается с уже упомянутыми максимумами. Нужно иметь ввиду, что при создании равномерной нагрузки кольца на зеркало цилиндра обеспечивается равномерный износ кольца и, как следствие, достигается наибольший ресурс работы колец.
Поршневые кольца изготавливаются из специального чугуна, редко — из стали. Чугунная заготовка, из которой изготавливаются кольца, не должна содержать пор, поэтому используется либо метод центробежного литья, либо так называемый метод наморозки. Для улучшения ресурсных показателей работы кольца, его поверхность может покрываться хромом (в основном верхние компрессионные и маслосъемные), а для лучшей прирабатываемости на рабочую поверхность колец иногда наносится тонкий слой олова. В современных ДВС часто используются компрессионные кольца с металлокерамическим напылением рабочей поверхности, которое обеспечивает высокую износостойкость и низкий коэффициент трения поверхностей.
Стык кольца может выполняться прямым или ступенчатым, что создает дополнительный лабиринт в уплотнении. Существует достаточно большое количество конструкций колец, выбор из которых выполняет конструктор двигателя. Самые простые в изготовлении компрессионные кольца — прямые (в сечении прямоугольник), однако большие ресурсы и лучшее уплотнение показывают трапециевидные кольца (в сечении – трапеция, равнобедренная или прямоугольная). Для того чтобы второе и последующие компрессионные кольца выполняли дополнительно функцию маслосъема, его изготавливают со скребком, возможна конструкция, когда кольцо при работе изгибается за счет изготовления внутренней односторонней фаски. С аналогичными целями часто используются так называемые минутные кольца, у которых рабочая поверхность скошена на конус с очень малым углом при вершине.
Основной съем масла с поверхности зеркала цилиндра производят специальные маслосъемные кольца, которые располагаются в поршневых канавках ниже компрессионных колец. Маслосъемные кольца могут быть цельной коробчатой конструкции, а могут быть составными, состоящими из двух и более элементов. Самая простая и распространенная конструкция маслосъемного кольца – коробчатая, которая имеет две скребковые части, между которыми выполняется проточка. По всей проточке с определенным шагом выфрезерованы сквозные сегменты для стока масла из пространства между скребками. Канавки под установку маслосъемных колец в поршне имеют ряд сверлений, выходящих во внутреннюю часть поршня (подпоршневое пространство цилиндра) для удаления снятого кольцом масла. При наличии обязательной глубокой проточки и сквозных фрезеровок, конструкция кольца теряет жесткость и может не обеспечить полное прилегание к поверхности цилиндра. В конструкции составного маслосъемного кольца такой недостаток устраняется за счет установки пружинного экспандера. Для этого собственную жесткость кольца максимально понижают, создавая полусферическую выборку с внутренней стороны кольца под установку экспандера. После монтажа в цилиндр, экспандер, находясь в сжатом состоянии, оказывает давление на кольцо, равномерно прижимая его к зеркалу цилиндра. Кроме описанных выше основных и самых распространенных конструкций маслосъемных колец существуют другие, которые называют наборными. Такие кольца состоят из двух тонких (более 1мм) стальных колец и одного или двух экспандеров. Экспандеры наборных колец одновременно прижимают тонкие кольца к торцевым поверхностям канавки в поршне и отжимают их к зеркалу цилиндра. Экспандеры представляют собой волнистые профили, изготовленные из пружинной стали, замки которых устанавливаются «в стык». Такие конструкции маслосъемных колец в основном находят применение в малоразмерных ВОД.
При установке поршня с установленными кольцами в цилиндр, стыки колец должны быть разведены, т.е. находится на разных образующих цилиндра поршня. Порядок разводки поршневых колец указывается в инструкциях по монтажу или, при отсутствии таковой, стыки колец разводятся на равные углы.
Теперь об особенностях установки колец в двухтактных двигателях. В то время как поршневые кольца в четырехтактном двигателе имеют некоторый дрейф и поэтому не проявляют склонность к потере подвижности или, так называемому «зависанию», в двухтактном двигателе все обстоит намного хуже. А именно, как мы уже знаем, в нижней части гильзы двухтактного двигателя размещаются продувочные окна, поэтому кольцо должно быть строго ориентировано таким образом, чтобы тепловой зазор – стык кольца не в коем случае не попал на окно, что вызовет деформацию кольца и его поломку при задевании о кромку окна. Для этого в поршневой канавке устанавливают стопор, который препятствует дрейфу кольца и поэтому кольцо, имея малую подвижность, склонно к зависанию.
Поршень шарнирно соединяется с шатуном в ВГШ посредством поршневого пальца. Поршневой палец передает на шатун действие газовой силы и является тяжелонагруженной деталью ДВС. Поскольку силы, возникающие в пальце – изгибающие, он выполняется в форме полого цилиндра. Материалом для поршневого пальца служат низколегированные, малоуглеродистые стали, которые могут быть подвергнуты поверхностной термохимической обработке с целью создания твердой износостойкой рабочей поверхности при сохранении мягкого и вязкого тела пальца. Рабочая поверхность пальца обрабатывается шлифованием с высокой точностью и чистотой поверхности. В серийном и массовом производстве двигателей сборка узла выполняется селективно.
Конструкция поршневого пальца определяется способом подвода смазки к узлам подшипников скольжения в поршне и ВГШ. Если смазка подшипников производится масляным туманом, то палец будет представлен в виде цилиндра с внутренним отверстием. Такая же конструкция будет использоваться в случае подвода смазки во втулку ВГШ принудительно через тело шатуна, в то время как смазка бобышек поршня осуществляется масляным туманом. Если же требуется производить смазку бобышек поршня под давлением, тогда втулка ВГШ имеет кольцевую проточку в зоне выхода масляного канала из тела шатуна, а палец имеет сверление (одно или несколько) напротив канавки с выходом во внутреннее отверстие. Также сверления в пальце делается в зоне контакта с бобышками поршня, а во внутренне отверстие пальца устанавливают торцевые заглушки. Таким образом, смазка под давлением из шатунного подшипника поступает по телу шатуна во втулку ВГШ, а затем, по отверстиям пальца к бобышкам поршня. Для уменьшения количества масла, находящегося во внутреннем отверстии поршневого пальца и, тем самым, уменьшения массы движущихся деталей и силы инерции возвратно- поступательно движущихся масс, в палец прессуется тонкостенная втулка в форме катушки, образующая кольцевую масляную полость.
Рассмотрим конструкцию газораспределительного механизма (ГРМ) четырехтактного ДВС. Механизм газораспределения четырехтактного двигателя состоит из кулачкового распределительного вала механизма газораспределения (распредвала) с подшипниками распредвала и механизмом привода, клапанов (впускных и выпускных), клапанных пружин с опорными тарелками и элементами стопорения, системы регулирования теплового зазора и деталей привода клапанов, которые передают движение от кулачков распредвала к клапанам.
Распределительный вал ГРМ, показанный на рис. 8.2. это набор кулачков, размещенных в строго определенном положении, в соответствии с требуемыми фазами газораспределения и последовательностью работы цилиндров.
Рис. 8.2. Распределительный вал механизма газораспределения
четырехтактного четырехцилиндрового двигателя
Так же, как и коленчатый вал, распределительный вал вращается в подшипниках скольжения, поэтому в определенных местах распредвала расположены опоры – шейки, которые устанавливаются в отверстия подшипника скольжения, расположенных в остове двигателя. При этом различают две конструкции двигателя по признаку расположения распредвала: если распределительный вал размещен в блоке цилиндров, то двигатель называют «с нижним распредвалом», если же вал ГРМ размещают в головке блока цилиндров или в деталях, расположенных на ней, то такие двигатели называются «с верхним распредвалом».
Привод распредвала выполняет функцию синхронизации вращения коленчатого и распределительного вала. На всех деталях привода установлены отметки и ориентирующие элементы, обеспечивающие сборку всего механизма только в одном положении с сохранением требуемых фаз газораспределения двигателя. Наиболее характерными способами передачи движения от коленвала к распредвалу являются: для двигателя с нижним расположением распредвала – шестеренный, с паразитною шестерней или без нее. Иногда для малоразмерных ВОД используют цепной привод. Для двигателя с верхним распредвалом используется три вида приводов – через валы и конические шестерни, цепной и с синхронизирующим зубчатым ремнем (последних два можно встретить только в малоразмерных высокооборотных двигателях). При использовании любого способа передачи вращения, основным требованием является обеспечение синхронности и сохранения передаточного отношения (не забываем, что распредвал вращается в два раза медленнее, чем коленчатый вал четырехтактного двигателя). Строгая ориентация элементов привода называется фазировкой двигателя. Не выполнение правил фазировки двигателя, равно как и нарушение ее в процессе работы моментально влечет за собой серьезную поломку двигателя в виде встречи поршня с открытыми клапанами, происходит поломка привода или изгиб клапана (возможны более серьезные поломки), цилиндры теряют компрессию, а двигатель полностью утрачивает работоспособность.
Подшипники скольжения распредвала, как правило, представляют собой разрезные биметаллические втулки, рис. 8.3, с основой и антифрикционным слоем, аналогичным вкладышам коленвала. В стыке разрезные втулки распредвала часто имеют фигурный замок, облегчающий установку их в постели. Втулки запрессовываются в отверстие – постель — с определенной ориентацией для совмещения отверстий, через которые подается смазка. В более ранних конструкциях дизелей можно встретить такое решение, когда распределительный вал вращается непосредственно в отверстиях корпусных деталей остова двигателя (без установки вкладышей), но такие конструктивные решения резко снижают ремонтопригодность.
Рис. 8.3. Втулки (вкладыши) подшипников распредвала
Отдельно необходимо остановиться на аспекте регулировки фаз газораспределения в современных дизелях. Дело в том, что конструкции современных двигателей могут включать в себя не один, а, как минимум, два распредвала, при этом каждый распредвал управляет своей группой клапанов, — впускных или выпускных. В этом случае появляется возможность (в зависимости от режима работы двигателя) выбирать наиболее оптимальные фазы газораспределения за счет использования специальных механизмов, вмонтированных в шестерню привода распредвала. Такие механизмы по команде электронного блока управления двигателем (ЭБУ) смещают на заданный угол распредвал относительно зубчатого венца шестерни, чем достигается изменение фаз газораспределения.
Кулачек распредвала приводит в действие механизм привода клапанов. Для двигателей с нижним расположением распредвала кулачек вала приводит в движение толкатель, который передает движение на штангу толкателя. Далее штанга толкателя воздействует на коромысло, которое, в свою очередь, нажимает на стержень клапана. Такова классическая схема. Рассмотрим отдельные элементы конструкции. Толкатель в самом простом случае представляет цилиндр с плоской торцевой поверхностью, внутри толкателя делается сферическая поверхность, на которую опирается ответная сфера штанги толкателя. Поскольку механизм газораспределения подвержен действию сил инерции, возникающих в результате постоянного изменения скорости движения деталей, пара трения кулачек распредвала – толкатель тщательно подбирается, а поверхности деталей проходят термохимическую или просто термическую обработку с целью увеличения твердости трущихся поверхностей. Толкатель установлен в расточку блока, причем ось отверстия смещена относительно кулачка, что вызывает вращение толкателя при работе и его равномерный износ. Такая конструкция ввиду специфики работы склонна к разрушению под действием контактных напряжений, что выражается в появлении каверн от выкрашивания материала на рабочей поверхности деталей. В тяжелонагруженных двигателях используют более сложную конструкцию толкателя с роликом, которая позволяет увеличить долговечность работы пары кулачек – толкатель, Необходимо иметь ввиду, что ролик должен занимать строго определенное угловое положение относительно кулачка распредвала, поскольку его поворот относительно оси вызовет моментальную поломку механизма. Поэтому роликовый толкатель должен иметь фиксатор от поворота. Конструкции роликовых толкателей нашли широкое применение в реверсивных дизелях.
Штанга толкателя это трубка с напрессованными по концам наконечниками со сферами (наружными или внутренними), которые опираются на ответные сферические поверхности толкателя и коромысла. Клапанные коромысла это рычаги (как правило, неравноплечие), которые имеют возможность качания на оси коромысел, закрепленных на головке блока или крышке цилиндра. Понятно, что каждому кулачку распредвала соответствует свой толкатель, штанга толкателя и коромысло. Если крышка цилиндра имеет компоновку с четырьмя клапанами (два впускных и два выпускных), то одно из плеч рычага клапанного коромысла выполняется в виде вилки. Также в этом случае возможны конструктивные варианты.
Оси коромысел качаются на подшипниках, в большинстве конструкций, это подшипники скольжения. Ось коромысел имеет поверхностную обработку на повышение твердости, а в отверстие коромысла устанавливаются биметаллические разрезные втулки (иногда тонкостенные бронзовые). Смазка в узел подшипника подается через ось коромысел. В коромысле клапана предусматривается возможность выполнения регулировки теплового зазора в клапане, который задается из соображений компенсации разности тепловых удлинений клапанов, деталей остова и деталей привода. Обычно этот узел представляет собой винт, вкручиваемый в тело коромысла и контргайка, при этом, в зависимости от конструктивного решения, винт может опираться как на толкатель, так и на клапан (возможно, через специальную шайбу).
По иному выглядит привод клапанов у двигателя с верхним расположением распредвала. Принципиально, такая компоновка двигателя позволяет уменьшить массу деталей привода и, таким образом, уменьшить нагрузки на детали от сил инерции ГРМ. Обращает на себя внимание разнообразие конструкций привода клапанов в верхнераспредвальных двигателях. Так распределительный вал ГРМ может открывать клапан посредством рычага, установленного на ось, также рычаг может опираться на сферическую опору, причем кулачек распредвала может работать как непосредственно по твердой поверхности рычага, так и по ролику, установленному в рычаг. Возможен вариант, когда кулачек распредвала воздействует непосредственно на клапан, без рычага. В этом случае клапана с пружинами устанавливаются в колодцах, которые являются направляющими для толкателей с плоским дном, по которым и работает распредвал. Хорошо известна конструкция, когда толкатель крепится непосредственно на клапан и является элементом узла регулировки теплового зазора.
Для минимизации инерционных нагрузок в конструкцию привода клапанов часто вводят узел компенсации тепловых удлинений деталей. Такой узел представляет гидроцилиндр с невозвратным клапаном и называется гидрокомпенсатором. Под действием давления масла и (или) пружины, установленной в цилиндре поршень выдвигается из цилиндра до полного выбирания всех зазоров в механизме привода клапанов. При начале движения деталей привода поршень нагружается, сжимая масло в цилиндре, невозвратный клапан закрывается и, вследствие несжимаемости масла, весь узел начинает работать как цельная деталь. После снятия нагрузки давление в гидрокомпенсаторе падает, невозвратный клапан открывается и дает возможность пополнить утечки масла из компенсатора, происшедшие за время рабочего хода. Перед установкой новых гидрокомпенсаторов либо из них нужно удалить консервирующее масло, либо оставить собранный механизм на определенное время для удаления излишков масла из гидрокомпенсаторов. Наиболее типичными местами установки гидрокомпенсаторов являются: толкатели ГРМ, вместо узла регулировки теплового зазора в коромыслах и опоры рычагов привода клапанов в двигателях с верхним распредвалом. Как уже отмечалось, гидрокомпесаторы позволяют обеспечить работу механизма без зазора, это означает, что начальная скорость открытия клапана минимальна, т.е. снижаются силы инерции в механизме, и, как следствие, уменьшаются износы деталей. Кроме того, при наличии гидрокомпенсации зазоров в клапанном механизме упрощается обслуживание двигателя и, что самое главное, обеспечивается постоянство фаз газораспределения вне зависимости от тепловых зазоров в клапанах. Однако система гидрокомпенсации тепловых зазоров имеет ряд недостатков, так она крайне требовательна к геометрии распределительного вала в части сохранении линии вала. Очевидно, что при возникновении прогиба вала, начальный диаметр кулачка (затылок кулачка) превращается в эксцентриковую шайбу, что влечет за собой приоткрывание клапана в тактах сжатия – расширения, разгерметизацию цилиндра и потерю работоспособности двигателя. Сами гидрокомпенсаторы крайне требовательны к качеству и к степени очистки масла, поскольку попадание любого включения масла под клапан моментально повлечет за собой выход из строя гидрокомпенсатора (по этой причине категорически запрещается контакт гидрокомпенсатора с магнитом). Кроме того, гидрокомпенсаторы должны работать при определенном давлении в масляной магистрали, поскольку при превышении рабочего давления гидрокомпенсатор способен преодолеть действие клапанной пружины и вызвать открытие клапана. Отсюда вытекают особые требования к точности работы редукционных клапанов системы смазки. Также нужно отметить тот факт, что гидрокомпенсатор имеет ограниченный рабочий ход, поэтому при проведении ремонтных мероприятий нужно контролировать всю конструкторскую цепь размеров, способных вывести гидрокомпенсатор за пределы рабочего диапазона.
Рассматривая механизм привода клапанов нельзя не упомянуть о уже существующих системах электронного управления открытием клапанов, и, не смотря на то, что они пока не имеют широкого распространения, можно предположить, что за ними будущее. Также нужно упомянуть о системах гидропривода клапанов, использующихся, в основном на МОД.
К клапанному механизм двигателя, рис. 8.4, относятся:
Рис. 8.4. Детали клапанного механизма
направляющие втулки клапанов, собственно клапана, клапанные пружины, тарелки пружин, стопорные элементы тарелок пружин (обычно сухари), и пр. Иногда под пружинами (или над ними) устанавливаются упорные подшипники качения, снижающие потери трения на скручивание пружин при их сжатии, а также способствующие повороту клапана на оси. Для поворота клапана в ряде конструкций клапанного механизма используют специальные механизмы с целью обеспечения равномерности износов уплотнительной фаски клапана и седла. В целях сокращения расхода масла через направляющие клапанов, в конструкцию двигателей с наддувом часто включают уплотнительные элементы в виде маслосъемных колпачков, надевающихся на направляющие клапана, маслоотбойных шайб и др.
Клапан двигателя является крайне тяжелонагруженной в тепловом отношении деталью, поскольку колебания температур у поверхности тарелки клапана может достигать в тяжелонагруженных двигателях 500 и более градусов. Мало того, выпускной клапан подвержен воздействию агрессивной среды, которой является отработавшие газы, особенно при работе двигателя на тяжелых топливах, содержащих ванадий. По этой причине клапаны изготавливаются из высокосортных жаропрочных аустенитных сталей, а рабочие фаски клапана могут иметь вплавки из безоксидной керамики. Стержень клапана, работающий в направляющей втулке клапана, обычно подвергается специальной обработке поверхности цилиндра с целью повышения износостойкости или хромируется. Торцевая часть клапана в месте контакта с коромыслом, должна имеет особо твердую износостойкую поверхность.
В дополнение, необходимо отметить, что клапан это одно из немногих мест в конструкции двигателя, где требуется использование дорогих материалов. Несмотря на очень высокие температуры, достигаемые в камере сгорания (и, в принципе, обеспечивающие высокую термодинамическую эффективность цикла), средние температуры деталей, благодаря цикличности работы двигателя, оказываются весьма умеренными, а это означает, что подавляющее большинство деталей может изготавливаться из простых, дешевых и технологичных конструкционных материалов. К сожалению, применительно к газотурбинным установкам этого сказать нельзя.
Место посадки и уплотнения клапана в огневом днище крышки или головки называют седлом. Седло выполнено прямо в канале (впускном и выпускном), оно может быть сменным, поскольку является быстроизнашиваемым элементом. Как правило, седла запрессовываются в расточку канала, хотя, встречаются конструкции, в которых седла устанавливаются на стопорящих устройствах по переходной посадке. Материал седла – высокопрочный чугун, бронза, а также композиционные горячепрессованные материалы.
Направляющие втулки клапана устанавливаются по прессовой посадке в расточку головки или крышки цилиндра (редко клапан работает просто в расточке головки). Втулки изготавливают из чугуна или бронзы, в последнее время получили распространение втулки, изготовленные методами порошковой металлургии. Внутренняя поверхность втулки может иметь не глубокую нарезку с крупным шагом для удержания масла, смазывающего клапан.
В заключении несколько слов о механизме газораспределения двухтактных двигателей. В самом простом и классическом случае механизм газораспределения двухтактного двигателя представляет собой продувочные окна, открытием которых управляет поршень. Очевидно, что при реализации петлевой продувки механизма, как такового, не существует. При использовании прямоточной продувки, в крышке цилиндра двигателя устанавливается клапан (клапана), обычно выпускной. В таком случае требуется включение в конструкцию двигателя механизма, управляющего открытием клапана. Этот механизм по своей конструкции мало отличен от конструкции ГРМ четырехтактного двигателя за тем отличием, что частота срабатывания клапанного механизма двухтактного двигателя составляет один раз за один оборот коленчатого вала.
Л е к ц и я № 9
ОСНОВНЫЕ СИСТЕМЫ СУДОВЫХ ДВС
Прежде чем приступить к изучению систем двигателей, необходимо констатировать, что все их рассматриваемые системы интегрированы в общие системы СЭУ и являются их неотъемлемой частью.
Системы двигателей внутреннего сгорания предназначены для обеспечения работы всех механизмов ДВС и двигателя вцелом. Рассмотрение систем начнем с системы смазки.
Система смазки выполняет функцию подачи масла ко всем узлам трения двигателя, а также производит съем тепла от ряда деталей двигателя, охлаждаемых маслом. Кроме того, смазывающее масло системы смазки выполняет функцию уплотнения деталей цилиндро-поршневой группы, а в межэксплуатационный период консервирует смазываемые детали.
Смазка деталей двигателя может осуществляться: под давлением, разбрызгиванием (барботажная смазка), за счет действия инерционных сил (черпаками, установленными на движущихся деталях) и лубрикаторным насосом, подающим масло на определенные трущиеся поверхности. Инерционные системы смазки в современных двигателях практически не используются (за исключением легких подвесных моторов), при этом они получили распространение в компрессорной технике и насосах. Лубрикаторные системы смазки находят применение в большеразмерных МОД, в основном, для смазки цилиндров. Смазка разбрызгиванием используется для деталей цилиндропоршневой группы всех поршневых ДВС (за исключением крейцкопфных МОД с лубрикаторной смазкой цилиндров), а также в отдельных конструкциях для смазки втулок ВГШ.
Рекомендуемые страницы:
Воспользуйтесь поиском по сайту:
megalektsii.ru
Поршневая группа: комплектация и устройство
Поршневая группа – это поршень и группа уплотняющих колец. Так же в неё входит поршневой палец и детали крепления. Стоит рассмотреть назначение данного механизма.
За счет него воспринимается давление газа и передается через шатун на коленвал. Так же благодаря такому механизму, как поршневая группа, уплотняется надпоршневая полость цилиндра. Таким образом он будет защищен от излишнего попадания в картер смазочного масла и газов. Данная функция имеет огромное значение для хорошей работы двигателя. О том, в каком техническом состоянии он находится, судят по уплотняющей способности. К примеру, в машинных двигателях не допускается, чтобы расход масла составлял больше, чем три процента от расхода горючего.
Поршневая группа свою работу осуществляет еще и в тяжелых климатических условиях. Именно поэтому детали данного механизма обладают высокой тепловой напряженностью, а это учитывается, когда для них выбирается материал и конструкция. Их элементы обычно производители разрабатывают, учитывая тип двигателей и назначение (транспортные, стационарные, дизельные, формированные и т.д.). Однако общее устройство все равно остается прежним. Итак, следует рассмотреть, из чего же комплектуется поршневая группа.
Тронковая часть (направляющая) еще называется поршневой юбкой. Она изнутри имеет приливы, в них просверлены отверстия для поршневого пальца. Нижняя кромка юбки используется часто как технологическая база при обработке поршня. Она для этого снабжена растачиваемым буртиком. Кроме того, стенки юбки еще воспринимают силы бокового давления, а это увеличивает их трение о цилиндровые стенки и повышает нагрев цилиндра и поршня.
Поршневая головка несет поршневые кольца и имеет днище. Нижняя канавка имеет дренажные отверстия, через них отходит смазочное масло, чтобы оно не попало случайно в камеру сгорания. Её днище – это одна из камерных стенок. Она воспринимает значительное давление газов. Само днище может быть плоским, вогнутым, выпуклым или фигурным. Опять-таки, его форма выбирается при учете типа двигателя, а также камеры сгорания.
Нельзя не упомянуть про такой механизм, как цилиндро-поршневая группа. Главные дефекты блоков цилиндра – это трещины, сколы и износ. Эти неисправности устанавливаются после тщательного осмотра, опрессовки и обмера цилиндра. При этом процессе на блок нужно установить головку или же чугунную плиту (обязательна резиновая прокладка). Вообще, данная группа отличается жаростойкой сталью и масляным охлаждением, которое осуществляется за счет циркуляционной общей системы смазки главного дизеля. Если обеспечить хороший уход механизму и качественное масло, то можно легко увеличить срок работы поршней и цилиндров.
И еще один механизм – шатунно-поршневая группа. Поршень – литой и алюминиевый. Наружная поверхность обладает весьма сложной формой. Поршневой палец – полый и стальной, он свободно вращается во втулке шатуна и поршневых бобышках. А кольца поршня выполнены из чугуна. И, конечно же, шатун – кованый и стальной. В его верхней головке имеется втулка из смеси стали и бронзы, что положительно отражается на работе всей группы.
fb.ru
Cпецдисциплина — Цилиндро-поршневая группа
Цилиндро-поршневая группа
Поршень. Служит для восприятия давления газов при рабочем ходе и осуществления вспомогательных тактов.
Представляет
собой перевернутый металлический стакан изготовленный из
высококремнистого алюминиевого сплава, в редких случаях из чугуна и еще
реже из сплавов на магниевой основе и из стали.
Поршень состоит из днища, головки (уплотняющей части) и направляющей части (юбка)
В
бензиновых двигателях головка поршня выполнена с плоским или выпуклым
днищем (а также есть поршни, днища которых исполняют вогнутыми и с
фигурными выемками) и имеет толстые стенки с внутренними ребрами,
повышающими ее прочность и отвод теплоты.
Часть юбки под бобышками
удалена для прохода противовесов коленчатого вала при нижнем положении
коленчатого вала и его облегчения. В поршнях имеются поперечные прорези
под головкой. Благодаря прорезям повышается упругость юбки поршня,
устраняется опасность заклинивания. В двигателе их размещают
соответственно надписи (обозначение), выполненной на юбке или днище
поршня, кроме того так же наносится размерная группа, размер поршня,
класс размера по пальцу, масса поршня
Рис. Днище поршня бензинового двигателя автомобиля ВАЗ 2105 указаны
Слева направо:
1. 2 — класс размера по пальцу
2. D — группа размера поршня (больше только Е)
3. ← — ориентация поршня в цилиндре (стрелкой в сторону шкива генератора)
4. Размер поршня
Рис. Поршень автомобиля КамАЗ
Днище
поршня дизельного двигателя делают с выемкой, форма которой зависит от
способа смесеобразования и расположения клапанов и форсунок.
На
внешней поверхности головки проточены канавки для компрессионных к и
маслосъемных колец. По окружности канавок под маслосъемные кольца
просверлены сквозные отверстия для отвода масла в картер двигателя
В
юбке поршня находятся приливы (бобышки) с отверстиями для поршневого
пальца в которых проточены кольцевые канавки для стопорных колец.
Для
предохранения поршня от заклинивания диаметр юбки больше диаметра
головки и юбка имеет овальное сечение (большая ось овала перпендикулярна
к оси поршневого пальца)
Рис. Устройство поршня.
1. днище поршня
2. головка поршня (уплотняющая часть)
3. направляющая часть (юбка)
4. выемка камеры сгорания
5. канавки для компрессионных и маслосъемных колец
6. прилив (бобышка) с отверстием
Поршневой
палец. Служит для шарнирного соединения поршня с верхней головкой
шатун. Изготавливают пустотелым из стали. Наружная поверхность
подвергается цементации и закаливается токами высокой частоты.
В
двигателе автомобиля КамАЗ, в отверстие втулки верхней головки шатуна
палец вставляют с зазором, а в поршень – с натягом. Во время работы
двигателя из-за различных коэффициентов линейного расширения материалов
между поршнем и пальцем при достижении рабочей температуры появляется
зазор, и палец может проворачиваться в бобышках поршня. Такой палец
называют плавающим.
В двигателе автомобиля ВАЗ, палец
запрессовывается в верхнюю головку шатуна с натягом, что исключает его
осевое перемещение в поршне. Поршневой палец свободно вращается в
бобышках поршня.
Рис. Поршневой палец автомобиля КамАЗ
Поршневые кольца. Уплотняют полость цилиндра, исключая прорыв газов в картер двигателя и попадания масла в камеру сгорания.
По назначению подразделяют на компрессионные и маслосъемные.
Компрессионные кольца изготавливают из легированного чугуна или стали.
На поршень устанавливают 2-3 компрессионных кольца.
Разрез
в поршневом кольце называют замком. Этот разрез позволяет кольцу
изменять наружный диаметр, что обеспечивает его плотное прилегание к
стенкам цилиндра. В рабочем состоянии зазор между концами замка должен
быть 0,2-0,35 мм. Для исключения проникновения газов через зазоры в
замках кольца устанавливают замками в разные стороны. В канавках поршня
кольца устанавливаются с небольшим зазором, и могут свободно
перемешаться относительно поршня.
Рис.
Расположение поршневых колец в канавках поршня: 1 – поршень; 2 –
верхнее компрессионное кольцо; 3 – нижнее компрессионное кольцо; 4 –
маслосъемное кольцо
Верхнее компрессионное кольцо хромированное
для повышения износостойкости. В поперечном сечении компрессионные
кольца могут быть различной формы. Некоторые из них имеют фаску или
выточку по внутреннему диаметру кольца. Нижнее компрессионное кольцо
имеет сечение скребкового типа и фосфатировано. Кроме основной функции,
оно выполняет также дополнительную – маслосбрасывающего кольца.
Маслосъемные кольца препятствуют проникновению масла из картера в камеру сгорания, снимая излишки масла со стенки цилиндра.
На
наружной поверхности имеется проточка и щелевые прорези для отвода во
внутреннюю полость поршня масла, снимаемого со стенок цилиндра. На
внутренней поверхности кольцо имеет канавку, в которой устанавливается
разжимная витая пружина, обеспечивающее дополнительное прижатие кольца к
стенкам цилиндра
Рис. Маслосъемное кольцо с разжимной витой пружиной
1. щелевые прорези
2. витая пружина
На поршни многих двигателей устанавливают составные маслосъемные кольца, изготовленные из двух плоских стальных колец и двух пружинных расширителей — осевого и радиального.
specsvv.ucoz.ru
Ликбез: ЦПГ- цилиндро-поршневая группа. | Все о бензопилах
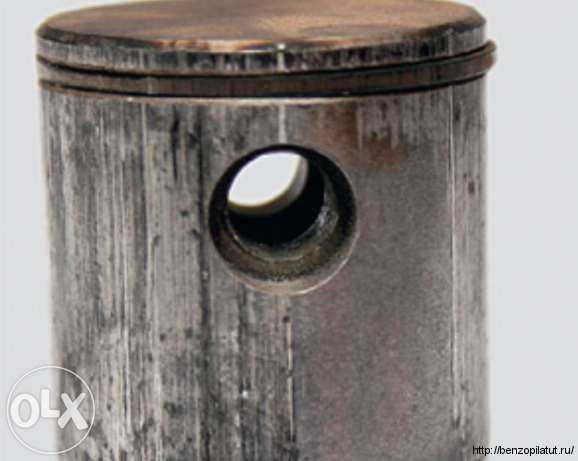
Сегодня поговорим о ЦПГ — цилиндро-поршневой группе. Поршень и цилиндр — главные составляющие двигателя бензопилы, а двигатель это ее «сердце». Поэтому при эксплуатации бензиновой пилы необходимо уделять внимание профилактике и контролю состояния цилиндро-поршневой группы постоянно. Кроме того, что неудовлетворительное ее состояние влияет на правильную работу пилы, ее мощность, приемистость и другие характеристики, так еще и стоимость ЦПГ часто может доходить до половины стоимости всей бензопилы. Так что уделим время этому важному узлу, расскажем, что входит в состав ЦПГ, рассмотрим неисправности, некоторые особенности ЦПГ бензопил.
ЦПГ бензопилы
Устройство ЦПГ
Итак, что входит в состав ЦПГ( цилиндро-поршневой группы):
- Поршень
- Цилиндр
- Кольца (маслосъемные и компрессионные)
ЦПГ это основной узел двигателя, неисправности которого неизбежно ведут к дорогостоящему ремонту. Для поддержания его в рабочем состоянии необходимо лишь четко следовать инструкции и соблюдать некоторые общие правила:
- Использовать качественные масла, разведенные в точной пропорции, которая указана производителем.
- Избегать перегрева двигателя.
- Соблюдать нормативы работы для класса бензопилы (бытовая, полупрофессиональная, профессиональная).
- Всегда использовать правильно наточенную цепь, установленную в нужном направлении.
Неисправности ЦПГ бензопилы:
- Износ поршня, цилиндра
- Износ колец
- Механические повреждения (скол колец, подшипника)
Все эти и другие не такие распространенные неисправности в итоге приводят к задирам на стенках цилиндра или поршня, что в свою очередь приводит к замене полностью цилиндро-поршневой группы.
Как диагностировать в результате чего возникли задиры?
Первым делом снимите глушитель и в образовавшемся окне осмотрите ЦПГ на предмет задиров.
Если задиры только со стороны глушителя, то это свидетельство того, что бензопилу перегрели.
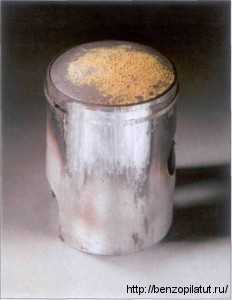
тепловой задир
Если задиры по всей окружности цилиндра и они равномерные и имеют большое истирание и темный цвет, то это свидетельство неправильно приготовленной топливной смеси.

задир при неправильной смеси
В случае если задиры имеют вид глубоких царапин, расположенных неравномерно, то это механические повреждения ЦПГ, которые возникают в случае попадания в цилиндр инородных тел или сколов деталей ЦПГ.
Задиры расположены в зоне кольца- плохое качество смеси. Так же возможно что пилу обкатывали «по-советски».
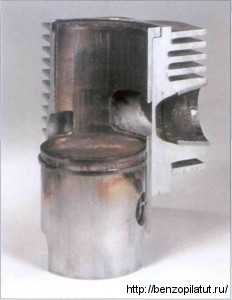
задир колец
Вот основные причины и виды неисправностей ЦПГ. Если у Вас есть вопросы, то задавайте их в комментариях или в группе ВК.
Вот неплохое видео о диагностике ЦПГ:
Вы можете помочь в составлении рейтинга бензопил, проголосовав в опросе: «Составляем рейтинг бензопил»
Мой мир
Вконтакте
Одноклассники
Google+
benzopilatut.ru
Поршень двигателя (назначение, устройство, принцип работы)
В цилиндро-поршневой группе (ЦПГ) происходит один из основных процессов, благодаря чему двигатель внутреннего сгорания функционирует: выделение энергии в результате сжигания топливовоздушной смеси, которая впоследствии преобразуется в механическое действие – вращение коленвала. Основной рабочий компонент ЦПГ — поршень. Благодаря ему создаются необходимые для сгорания смеси условия. Поршень — первый компонент, участвующий в преобразовании получаемой энергии.
Поршень двигателя имеет цилиндрическую форму. Располагается он в гильзе цилиндра двигателя, это подвижный элемент – в процессе работы он совершает возвратно-поступательные движения и выполняет две функции.
- При поступательном движении поршень уменьшает объем камеры сгорания, сжимая топливную смесь, что необходимо для процесса сгорания (в дизельных моторах воспламенение смеси и вовсе происходит от ее сильного сжатия).
- После воспламенения топливовоздушной смеси в камере сгорания резко возрастает давление. Стремясь увеличить объем, оно выталкивает поршень обратно, и он совершает возвратное движение, передающееся через шатун коленвалу.
Что такое поршень двигателя внутреннего сгорания автомобиля?
data-full-width-responsive=»true»>
Содержание статьи
Устройство детали включает в себя три составляющие:
- Днище.
- Уплотняющая часть.
- Юбка.
Указанные составляющие имеются как в цельнолитых поршнях (самый распространенный вариант), так и в составных деталях.
Днище
Днище — основная рабочая поверхность, поскольку она, стенки гильзы и головка блока формируют камеру сгорания, в которой и происходит сжигание топливной смеси.
Главный параметр днища — форма, которая зависит от типа двигателя внутреннего сгорания (ДВС) и его конструктивных особенностей.
В двухтактных двигателях применяются поршни, у которых днище сферической формы – выступ днища, это повышает эффективность наполнения камеры сгорания смесью и отвод отработанных газов.
В четырехтактных бензиновых моторах днище плоское или вогнутое. Дополнительно на поверхности проделываются технические углубления – выемки под клапанные тарелки (устраняют вероятность столкновения поршня с клапаном), углубления для улучшения смесеобразования.
В дизельных моторах углубления в днище наиболее габаритны и имеют разную форму. Такие выемки называются поршневой камерой сгорания и предназначены они для создания завихрений при подаче воздуха и топлива в цилиндр, чтобы обеспечить лучшее смешивание.
Уплотняющая часть предназначена для установки специальных колец (компрессионных и маслосъемных), задача которых — устранять зазор между поршнем и стенкой гильзы, препятствуя прорыву рабочих газов в подпоршневое пространство и смазки – в камеру сгорания (эти факторы снижают КПД мотора). Это обеспечивает отвод тепла от поршня к гильзе.
Уплотняющая часть
Уплотняющая часть включает в себя проточки в цилиндрической поверхности поршня — канавки, расположенные за днищем, и перемычки между канавками. В двухтактных двигателях в проточки дополнительно помещены специальные вставки, в которые упираются замки колец. Эти вставки необходимы для исключения вероятности проворачивания колец и попадания их замков во впускные и выпускные окна, что может стать причиной их разрушения.
Перемычка от кромки днища и до первого кольца именуется жаровым поясом. Этот пояс воспринимает на себя наибольшее температурное воздействие, поэтому высота его подбирается, исходя из рабочих условий, создаваемых внутри камеры сгорания, и материала изготовления поршня.
Число канавок, проделанных на уплотняющей части, соответствует количеству поршневых колец (а их может использоваться 2 — 6). Наиболее же распространена конструкция с тремя кольцами — двумя компрессионными и одним маслосъемным.
В канавке под маслосъемное кольцо проделываются отверстия для стека масла, которое снимается кольцом со стенки гильзы.
Вместе с днищем уплотнительная часть формирует головку поршня.
Вас также заинтересует:
Юбка
Юбка выполняет роль направляющей для поршня, не давая ему изменить положение относительно цилиндра и обеспечивая только возвратно-поступательное движение детали. Благодаря этой составляющей осуществляется подвижное соединение поршня с шатуном.
Для соединения в юбке проделаны отверстия для установки поршневого пальца. Чтобы повысить прочность в месте контакта пальца, с внутренней стороны юбки изготовлены специальные массивные наплывы, именуемые бобышками.
Для фиксации пальца в поршне в установочных отверстиях под него предусмотрены проточки для стопорных колец.
Типы поршней
В двигателях внутреннего сгорания применяется два типа поршней, различающихся по конструктивному устройству – цельные и составные.
Цельные детали изготавливаются путем литья с последующей механической обработкой. В процессе литья из металла создается заготовка, которой придается общая форма детали. Далее на металлообрабатывающих станках в полученной заготовке обрабатываются рабочие поверхности, нарезаются канавки под кольца, проделываются технологические отверстия и углубления.
В составных элементах головка и юбка разделены, и в единую конструкцию они собираются в процессе установки на двигатель. Причем сборка в одну деталь осуществляется при соединении поршня с шатуном. Для этого, помимо отверстий под палец в юбке, на головке имеются специальные проушины.
Достоинство составных поршней — возможность комбинирования материалов изготовления, что повышает эксплуатационные качества детали.
Материалы изготовления
В качестве материала изготовления для цельнолитых поршней используются алюминиевые сплавы. Детали из таких сплавов характеризуются малым весом и хорошей теплопроводностью. Но при этом алюминий не является высокопрочным и жаростойким материалом, что ограничивает использование поршней из него.
Литые поршни изготавливаются и из чугуна. Этот материал прочный и устойчивый к высоким температурам. Недостатком их является значительная масса и слабая теплопроводность, что приводит к сильному нагреву поршней в процессе работы двигателя. Из-за этого их не используют на бензиновых моторах, поскольку высокая температура становится причиной возникновения калильного зажигания (топливовоздушная смесь воспламеняется от контакта с разогретыми поверхностями, а не от искры свечи зажигания).
Конструкция составных поршней позволяет комбинировать между собой указанные материалы. В таких элементах юбка изготавливается из алюминиевых сплавов, что обеспечивает хорошую теплопроводность, а головка – из жаропрочной стали или чугуна.
Но и у элементов составного типа есть недостатки, среди которых:
- возможность использования только в дизельных двигателях;
- больший вес по сравнению с литыми алюминиевыми;
- необходимость использования поршневых колец из жаростойких материалов;
- более высокая цена;
Из-за этих особенностей сфера использования составных поршней ограничена, их применяют только на крупноразмерных дизельных двигателях.
Видео: Принцип работы поршня двигателя. Устройство
avtomotoprof.ru