состав и свойства — Информация
Пластиковый корпус и два контакта для подключения проводов. Именно так представляется автомобильный аккумулятор большинству из современных владельцев авто. Однако чтобы эксплуатировать его максимально эффективно, безопасно и без неожиданных сюрпризов, о батарее стоит знать немного больше.
Сегодня речь пойдет о столь важной составляющей конструкции авто и мото аккумуляторов, как электролит. Он представляет собой раствор серной кислоты, которая считается, пожалуй, одним из ключевых химических соединений в мире. Это обусловлено широким спектром ее применения. Раствор серной кислоты продается под различными наименованиями, которые зависят от степени крепости, а также уровня чистоты. Приведем несколько распространенных примеров:
- Камерная кислота – раствор серной кислоты с водой в пропорции от 60:40 до 70:30.
- Башенная кислота – раствор с соотношением от 75:25 до 82:18.
- Купоросное масло с содержанием серной кислоты до 97%.
- 100% серная кислота – моногидрат.
Если говорить о максимальной крепости, получаемой способом выпаривания, то этот параметр может достигать 98,5%. Однако для заправки аккумуляторных батарей ключевое значение приобретает чистота растворов купоросного масла с химической точки зрения.
Отметим также, что концентрированной серной кислотой называется совершенно прозрачная жидкость, не имеющая ни цвета, ни запаха. Она обладает консистенцию легкого масла. Ее удельный вес составляет 1б84 при температуре 15°С. В ней содержится примерно 95% серной кислоты. Концентрат может смешиваться с водой в любой пропорции. Изготавливая электролит в бытовых условиях, следует помнить, что смешивание воды и кислоты вызывает выделение значительного количества тепла. Температура кипения концентрированной серной кислоты составляет 338 градусов Цельсия.
Интересным фактом из курса химии является сокращение объема раствора. Примечательно то, что при смешении двух объемов серной кислоты и воды, соответственно, их итоговый объем будет меньше, чем суммарный.
Также обратите внимание на то, что удельный вес или плотность электролита авто или мото аккумулятора имеет непосредственную зависимость от тех температур, при которых работают аккумуляторы. Так, при эксплуатации в условиях низких температур нужен более плотный электролит. А в жарких странах – напротив – плотность электролита сознательно снижается. Это объясняется тем, что при таких температурах существенно повышается химическая активность раствора.
В заключение отметим, что плотность электролита также зависит от того, в каких режимах эксплуатируется батарея. Так, данный параметр для тяговых аккумуляторов обычно составляет 1.26 кг\с м³ , пусковые и осветительные источники питания имеют плотность до 1.3 кг\с м³ и т.д. Для автомобильных аккумуляторных батарей эта характеристика читается нормой, когда составляет 1.28 кг\с м³ .
23.08.2013, 59488 просмотров.
www.akb-market.ru
Состав электролитов железнения и его режимы
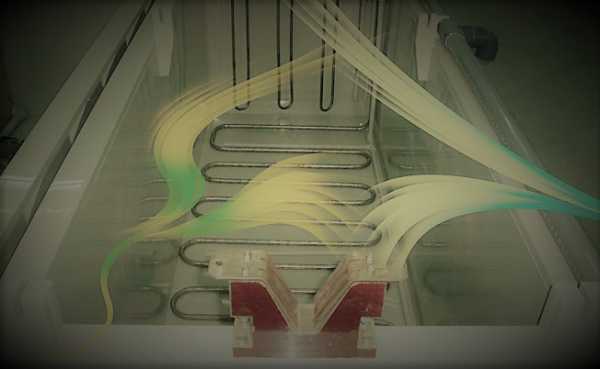
Осаждение железа ведут в ваннах, изготовленных из листовой стали, с пароводяной рубашкой, аналогично ваннам хромирования, но футеровку внутренней поверхности производить антег-митовыми плитками.
Существующие электролиты для железнения подразделяются на:
- хлористые;
- сернокислые;
- смешанные.
Кроме того, могут применяться борфтористоводородные, сульфаматные и прочие электролиты с различными добавками для повышения блеска, твердости и получения специальных свойств.
По способу применения процессы железнения подразделяют на холодные и горячие. В холодных электролитах (20-50 °С) процесс железнения проводят при малой плотности тока. Скорость осаждения металла в этих электролитах не превышает 100-130 мкм/ч. В горячих электролитах, нагретых до 50-105 °С, электролиз протекает при высоких плотностях тока (1020 А/дм
Резкие колебания температуры при железнении в горячих электролитах могут вызвать колебания напряжений по толщине слоя осадков. Поэтому возможно растрескивание и отслаивание покрытия. При наращивании деталей нельзя допускать колебаний температуры более ±2 °С. Колебания плотности тока в меньшей степени влияют на изменение свойств покрытия, чем температура. Однако желательно, чтобы не было и значительных колебаний плотности тока.
При осаждении электролитического железа необходимо избегать выключения тока. При длительной работе с перерывами тока следует перед каждым продолжением осаждения проводить анодную обработку детали в том же электролите в течение 1-2 мин при плотности тока 30-40 А/дм
Процесс покрытия электролитическим железом осуществляют с использованием растворимых (стальных) и нерастворимых (угольных) электродов. При наращивании слоя покрытия с помощью нерастворимых электродов необходимо систематическое корректирование состава электролита по мере истощения раствора.
Хлористые электролиты
Наибольшее применение получили хлористые электролиты, отличающиеся высокой концентрацией солей, большой скоростью наращивания железа и возможностью получения покрытий с большой толщиной. Эти электролиты получили применение на авторемонтных и других заводах для восстановления размеров на деталях, получивших большой износ.
Основным компонентом хлористого электродита для железнения является хлористое железо. Хлористое железо FeCl2*4Н2О — светло-зеленые кристаллы, растворимость — свыше 600 г/л при 20 °С, молекулярная масса 198,9. При нагревании растворимость еще более возрастает. Соль легко подвергается гидролизу, и ее растворы всегда следует подкислять соляной кислотой в количествах до 0,5-0,7 г/л. При высокой концентрации хлористого железа в хлористом электролите, состоящем в основном лишь из хлористого железа, концентрацию его растворов легко определить по плотности.
Для горячих хлористых электролитов разработано много вариантов с введением в их состав хлористого марганца, хлористого никеля, гипофосфита натрия и других солей. Составы и режимы осаждения железа приведены в табл. 5.3.
Электролит должен быть прозрачным, иметь зеленый цвет. Фильтровать его следует не реже одного раза в 10-15 сут при работе в две смены.
Твердость полученного слоя железа определяется температурой электролита и может изменяться от 100 до 400 НВ. В хлористых электролитах твердость осажденного железа возрастает с уменьшением концентрации хлористого железа и соляной кислоты, а также при увеличении катодной плотности тока и понижении температуры электролита.
Температура электролита оказывает наиболее существенное влияние на твердость осажденного покрытия. Так, в хлористом электролите (400 г/л FeCl2, 10 г/л NaCl и 1 г/л НСl) при понижении его температуры всего на 10 °С твердость осадка повышается на 40-60 единиц. При дальнейшем снижении температуры до 75 °С твердость повышается до 300 НВ. При регулировании твердости покрытия за счет температуры электролита следует учитывать, что чрезмерное понижение температуры приводит к растрескиванию и скалыванию наращенного слоя.
Таблица 5.3. Составы хлористых электролитов и режимы железнения.
Компоненты электролита и режимы процесса |
Составы электролита, г/л |
|||
1 |
2 |
3 |
4 |
|
Хлористое железо |
200-250 |
300-350 |
600-680 |
200-300 |
|
— |
— |
— |
20-30 |
Хлористый натрий |
100 |
— |
— |
— |
Соляная кислота |
— |
— |
— |
0,5-1,0 |
Кислотность рН |
0,8-1,2 |
0,8-1,2 |
0,8-1,5 |
— |
Температура электролита, °С |
70-80 |
70-80 |
70-80 |
60-80 |
Плотность тока, А/дм2 |
20-40 |
20-50 |
20-60 |
30-50 |
Выход по току, % |
85-92 |
85-95 |
85-95 |
90-95 |
Для катодного осадка электролитического железа характерны значительные внутренние напряжения. При железнении в хлористых электролитах при температуре 95 °С и плотности тока 5 А/дм2 остаточные напряжения в осажденном железе составляют примерно 150 МПа. При увеличении плотности тока до 20 А/дм2 напряжения возрастают до 370 МПа. Отпуск деталей, покрытых электролитическим железом, при температуре 500-600 °С уменьшает остаточные напряжения на 15-20 %. В электролитическом железе, полученном из хлористых электролитов при температуре 100 °С, содержится лишь 0,002-0,003 % водорода.
Сернокислые электролиты
При осаждении в сернокислых электролитах получают более хрупкие и крупнокристаллические осадки, чем в хлористых. Пластичные осадки железа в сернокислых ваннах образуются при нормальной температуре и низких плотностях тока (0,1-0,2 А/дм2). Электролитическое железо, осажденное из сернокислых растворов при 18 °С, содержит 0,085 % водорода, а твердость — 200-300 НВ.
Из сернокислых электролитов, применяемых на практике, наибольшее распространение получили растворы, в которых процесс производится без нагрева электролита или при небольшом повышении температуры. Для них также необходима анодная обработка деталей перед покрытием, как это указано при осаждении железа из хлористых электролитов (табл. 5.4).
Сернокислые и хлористые электролиты при повышенной температуре агрессивны к металлам оснастки ванны.
Процесс наращивания элемента детали железом, упрощается при применении борфтористоводородных электролитов следующего состава (г/л) и режимов:
борфтористоводородное железо — 300; борная кислота — 18;
свободная борфтористоводородная кислота — 1-2; температура, °С — до 20-60; плотность тока, А/дм2 — 2-12; кислотность рН — 3,5.
Таблица 5.4. Составы хлористых электролитов и режимы железнения.
Компоненты электролита и режимы процесса |
Составы электролита, г/л |
||
1 |
2 |
3 |
|
Сернокислое железо |
180-200 |
3150 |
200-450 |
Сернокислый магний |
40-50 |
— |
— |
Сернокислый натрий |
— |
100 |
— |
Двууглекислый натрий |
25-30 |
— |
— |
Серная кислота |
— |
1 |
— |
Борная кислота |
— |
— |
10-20 |
Борфтористоводородный калий |
— |
— |
20-35 |
Кислотность рН |
— |
2,4-2,5 |
1,9-2,4 |
Температура электролита, °С |
18-20 |
60-70 |
18-25 |
Плотность тока, А/дм2 |
0,1-0,15 |
5-10 |
До 7,0 |
Выход по току, % |
— |
— |
70-95 |
Таблица 5.5. Скорость осаждения железа при различных значениях плотности тока и выхода по току.
Плотность тока, А/дм2 |
Катодный выход по току, % |
|||
90 |
92 |
94 |
95 |
|
1 |
12,0 |
12,3 |
12,5 |
12,7 |
5 |
60,1 |
61,5 |
62,9 |
63,6 |
10 |
120,0 |
123,0 |
125,2 |
126,8 |
30 |
360,0 |
369,0 |
375,6 |
380,4 |
50 |
601,0 |
615,0 |
629,0 |
635,0 |
Электролит устойчив против окисления и характеризуется хорошей рассеивающей способностью. При наличии перемешивания электролита допускается увеличение плотности тока в 1,2—1,5 раза.
Скорость осаждения железа можно ориентировочно определить по табл. 5.5.
Возможно Вас так же заинтересуют следующие статьи: comments powered by HyperCommentsecm-zink.ru
Приготовление электролита | Аккумуляторные батареи
Страница 14 из 26
4.3. Приготовление электролита для свинцовых аккумуляторов
Электролит для свинцовых аккумуляторов приготовляется путем разбавления чистой серной кислоты чистой водой. Кислота продается обычно концентрированной, удельного веса от 1,835 до 1,840. При разбавлении концентрированной кислоты раствор сильно нагревается. Во избежание опасности для лица, производящего смешивание, всегда необходимо наливать кислоту в воду, но не наоборот.
Хотя количество теплоты, развиваемой в обоих случаях, одно и то же, однако удельные теплоты воды и концентрированной кислоты совершенно различны. Струя воды, попадая в концентрированную кислоту, освобождает большое количество теплоты, которая благодаря низкой удельной теплоте кислоты вызывает сильное местное повышение температуры. Кислота, приливаемая к воде, не может вызвать столь же большого повышения температуры в силу того, что удельная теплота воды очень высока. Необходимо непрерывно перемешивать раствор все время, пока кислота подливается в воду, для того, чтобы помешать более тяжелой кислоте опуститься на дно сосуда, не смешавшись с водой.
Для смешивания и хранения небольших количеств электролита наиболее подходят сосуды фарфоровые, гончарные или стеклянные; но так как они легко дают трещины, то им следует предпочесть чаны, выложенные свинцом, особенно для более значительных количеств.
Никакие другие металлические сосуды, кроме свинцовых, непригодны.
После разбавления кислоты, до заливки ее в батарею, необходимо подождать, пока она остынет, для того чтобы избежать повреждений пластин и сепараторов.
Охлаждение можно ускорить, пользуясь струей сжатого воздуха, но воздух при этом должен быть чистым.
Избежать сильного повышения температуры при смешивании кислоты с водой можно, применяя вместо воды лед, приготовленный из дистиллированной воды. Понижение температуры происходит вследствие того, что скрытая теплота плавления льда приблизительно равна количеству теплоты, освобождающемуся при растворении серной кислоты. Лед, свободный от воды, можно прибавлять к кислоте непосредственно. Избыток поглощенной теплоты показывает, что раствор должен получить температуру ниже нуля, что и наблюдалось в действительности.
Чтобы облегчить приготовление электролитов любой требуемой концентрации, на рис. 4.1 приведены необходимые пропорции кислоты и воды. Аккумуляторные заводы обычно сообщают сведения о том, какой крепости кислоту следует применять для каждой данной батареи.
Рис. 4.1. Приготовление электролита любого удельного веса из концентрированной кислоты удельного веса 1,835.
1- содержание серной кислоты, %; 2 – требующаяся добавка воды по объему; 3 – то же по весу.
4.4. Приготовление электролита для кадмиевоникелевых и железоникелевых аккумуляторов
Для кадмиевоникелевых и железоникелевых аккумуляторов в качестве электролита служит раствор в дистиллированной воде едкого калия (КОН) или едкого натрия (NaOH).
В зависимости от температуры окружающего воздуха в аккумуляторах (табл. 4.1) применяется раствор соответствующей плотности (концентрации) основного компонента электролита в чистом виде или с добавкой едкого лития (LiOH).
Кадмиевоникелевые аккумуляторы рассчитаны на работу на холоде при температуре до – 40°С, причем при температурах +35…– 19°С с составным электролитом, а при более низких температурах, например, – 20…– 40°С с электролитом без добавки едкого лития.
При температурах – 20…– 40°С при отсутствии чистого едкого калия допускается как исключение применять составной электролит из едкого калия и едкого лития повышенной плотности, при этом емкость аккумулятора снижается на 10 – 15%. При отсутствии составного электролита из едкого калия и едкого лития при температуре – 19…+35°С можно воспользоваться составным электролитом из едкого натрия повышенной плотности 1,17 – 1,19 г/см3 с добавкой на 1 л раствора 20 г едкого лития, но при этом следует учесть, не гарантируется.
Таблица 4.1.
Рекомендуемые состав и плотность электролита для кадмиевоникелевых и железоникелевых аккумуляторов при различной температуре окружающего воздуха
Температура воздуха, °С |
Рекомендуемый состав электролита |
Плотность, г/см3 |
– 19… +35 |
Составной раствор едкого калия с добавкой на 1 л раствора 20 г едкого лития аккумуляторного (моногидрата лития) |
1,19 – 1,21 |
– 20… – 40 |
Раствор едкого калия |
1,25 – 1,27 |
+10…+50 |
Раствор едкого натрия с добавкой на 1 л раствора 15 – 20 г едкого лития (моногидрата лития) |
1,1 – 1,12 |
Не гарантируется также долговечность аккумуляторов при работе их с электролитом из раствора чистого едкого калия плотностью 1,19 – 1,21 г/см3, т. е. без добавки едкого лития при температуре –19… + 10°С. При работе при температуре + 10…+50°С с рекомендуемым составным электролитом плотностью 1,1–1,12 г/см3 (табл. 5.1) емкость аккумуляторов также снижается по сравнению с номинальной, а долговечность не гарантируется.
Железоникелевые аккумуляторы рассчитаны на работу в тех же условиях и с тем же электролитом, что и кадмиевоникелевые, но они более чувствительны к низким температурам, поэтому могут применяться при температурах не ниже –20° С.
В процессе эксплуатации температурные условия в зависимости от времени года резко изменяются, поэтому для более эффективного использования емкости аккумуляторов их следует заливать электролитом, по составу и плотности соответствующим этим условиям.
Кроме того, необходимо систематически контролировать количество электролита, т. е. следить за уровнем последнего и поддерживать его в установленных пределах.
В аккумуляторах, находящихся в эксплуатации, уровень электролита постепенно снижается вследствие испарения, поэтому его необходимо периодически измерять и при необходимости дополнять до нормы дистиллированной водой. Не реже чем через 10 циклов нужно проверять плотность электролита и также доводить ее до нормы добавлением раствора плотностью 1,41 г/см3 или дистиллированной воды.
Уровень электролита в аккумуляторах должен постоянно находиться выше края пластин не менее чем на 5 мм и не более чем на 12 мм.
Снижение уровня электролита ниже верхнего края пластин или сетки, а также повышение плотности электролита при положительных температурах окружающего воздуха снижают емкость и долговечность последних. Уровень электролита необходимо проверять и доводить до указанной нормы перед каждым зарядом. Он проверяется с помощью стеклянной трубки диаметром 5 – 6 мм с метками на высоте 5 и 12 мм от конца. Для установления уровня электролита в аккумуляторе надо конец трубки с метками ввести через заливное отверстие до упора в пластины или сетку, после чего другой конец трубки закрыть пальцем. Вынув трубку из аккумулятора по высоте столбика электролита в ней, определим уровень электролита над верхним краем пластин или сетки в аккумуляторе. Для снижения уровня электролита в аккумуляторе можно пользоваться пипеткой или резиновой грушей со стеклянным или пластмассовым наконечником длиной около 100 мм. Доливку электролита или дистиллированной воды в аккумуляторы можно производить с помощью пипетки, резиновой груши или кружки через стеклянную воронку, размеры которых подбирают в зависимости от вместимости аккумуляторов. Проверка плотности электролита производится при помощи сифонного ареометра.
Проверку плотности электролита необходимо производить по возможности перед каждым зарядом, в каждом аккумуляторе, хотя и допускается выборочный контроль в 2 – 3 аккумуляторах батареи. В крайнем случае проверка должна проводиться не реже чем через 10 циклов во всех аккумуляторах батареи.
Таким образом, электролит необходим не только для первой заливки аккумуляторов при формировке, но и для замены, поддержания плотности и уровня электролита в действующих аккумуляторах, поэтому его требуется приготовлять и всегда иметь запас.
Для приготовления электролита поставляются следующие исходные материалы:
а) едкий калий аккумуляторный марки А (твердый) или марки В (жидкий) и едкий литий аккумуляторный;
б) составная щелочь сорта А – готовая смесь едкого калия и едкого лития в отношении едкий литий/едкий калий = 0,04…0,045;
в) едкий натрий аккумуляторный (сода каустическая) сорта А и едкий литий аккумуляторный;
г) составная щелочь сорта Б – готовая смесь едкого натрия и едкого лития в соотношении едкий литий/едкий натрий = 0,028…0,032.
Перед приготовлением электролита необходимо удостовериться, что имеющиеся в наличии химические ‘компоненты соответствуют приведенным выше требованиям и ГОСТам. Хранить эти материалы необходимо в герметически закрытой таре. Данные материалы могут поставляться как в жидком, так и в твердом состоянии в виде гранул, чешуек, кусков или слитка.
Приготовление электролита следует начинать с определения потребности в нем согласно норме расхода на один аккумулятор при первой заливке, указанной в табл. 4.2.
Определив требуемое количество электролита, приготовим примерно 3/4 этого объема свежей дистиллированной воды. При отсутствии последней допускается применение дождевой воды, собранной с чистой поверхности, или воды, полученной при таянии снега, а также конденсата.
Таблица 4.2
Ориентировочная норма расхода электролита на один аккумулятор при первой заливке
Тип |
Норма расхода электролита при первой заливке, л |
Тип |
Норма расхода электролита при первой заливке, л |
АКН-2,25 |
0,04 |
КН-60 |
0,75 |
Примечание. При приготовлении электролита желательно норму увеличить на 10 – 15 % для создания резерва на отход и другие непредвиденные случаи.
В крайнем случае можно использовать любую сырую чистую питьевую воду (кроме минеральной).
Затем, пользуясь данными табл. 5.3, определяем необходимое количество химических компонентов: едкого калия или едкого натрия, а также едкого лития для добавки. Расход дистиллированной воды на 1 кг твердой и на 1 л жидкой щелочи для приготовления электролита необходимой плотности приведен в табл. 4.3.
Таблица 4.3
Расход дистиллированной воды, необходимой для приготовления электролита для кадмиевоникелевых и железоникелевых аккумуляторов
Щелочь |
Плотность, г/смз3 |
Количество воды, л |
|
на 1 кг твердой щелочи |
на 1 кг жидкой щелочи плотностью 1,41 г/см3 |
||
Калиевая или готовая составная, т. е. с добавкой едкого лития Калиево-литиевая Натриевая или готовая составная натриево-литиевая |
1,19 – 1,21 1,25 – 1,27
1,17– 1,19 |
3 2
5 |
1 0,55
1,5 |
Для определения массы твердых щелочей, необходимой по норме, приведенной в табл. 19, достаточно разделить:
на три требуемое количество воды, если необходимо приготовить калиевый или составной калиево-литиевый раствор плотностью 1,19 – 1,21 г/см3;
на два, если необходимо приготовить калиевый электролит для работы при температуре
– 20…– 40° С или составной калиево-литиевый плотностью 1,25 –1,27 г/см3;
на пять, если необходимо приготовить натриевый или составной натриево-литиевый электролит плотностью 1,17 – 1,19 г/см3.
Если составная калиево-литиевая или натриево-литиевая щелочь отсутствуют, а имеется едкий калий, едкий натрий и едкий литий, то расчет потребности в твердых щелочах производится по тому же принципу, как указано выше. Следует иметь в виду, что в частном, полученном в результате деления, учитывается и масса едкого лития.
leg.co.ua
Электролит состав — Справочник химика 21
Электролит Состав, % (масс.) Темпе- ратура начала Плотность Удельная электро- [c.236]Кроме того, применяют электролит, состав которого следующий (г/л) [c.115]
Гликолевый электролит. Состав электролита (в г/л) [c.178]
Электролит Состав электролита Dk, а дм Температура, [c.76]
В. Ф. Молчанов [626] провел испытания на усталостную прочность образцов из стали 45 диаметром 9,48 мм на машине МУИ-6000 после хромирования в саморегулирующемся электролите (состав см. в табл. 6.1). Сталь имела состав (%) 0 46 С 0,28 51 0,65 Мп 0,023 5 0,21 Р 0,14 Сг 0,15 N1. Механические свойства стали 0т=465 МН/м (47,4 кГ/мм ), 0в=723 МН/м (73,8 кГ/мм ), 05 = 22%, а1) = 40,6%. Заготовки образцов подвергались нормализации при 850°С в течение 20 мин. Всего было испытано 10 серий образцов (табл. 6.6), каждая по 6—7 образцов. Толщина покрытия во всех сериях составляла 0,05 мм, кроме серии № 5 (0,3 мм). Кривые усталости приведены на рис. 6.1. [c.260]
Фнг. 30. Содержание цинка в латуни. (/) и олова в бронзе (2) в зависимости от концентрации свободного цианида в электролите. Состав электролита латунирования 16 Г/л Си и 16 Г/л 2п плотность тока 0,5 а/дм , температура 20°. [c.59]
Рецептура и режим работы ванн.. Для цинкования электродов серебряно-цинковых источников тока применяется цианистый электролит. Состав электролита и режим работы ванны следующие [c.45]
Золочение в цианистом электролите. Состав цианистого электролита и режим работы следующие [c.162]
Электрохимическое полирование. Электрохимическое полирование —- процесс выравнивания поверхности металла путем анодного растворения и применяется для повышения качества поверхности металлических изделий в дополнение к механическому шлифованию и полированию. Обрабатываемые детали завешиваются в ванну с электролитом в качестве анодов, катодами служат электроды из таких металлов, которые не растворяются в данном электролите. Состав электролита и режим процесса должны обеспечивать преимущественное растворение микроскопических выступов поверхности, в результате чего поверхность становится гладкой и приобретает блеск. При электрополировании решающую роль играет плотность тока, которая значительно выше, чем применяемая при осаждении металла. [c.138]
Закон Фарадея может быть использован для точного определения количества электричества, проходящего в цепи постоянного тока. Для этого нужно заставить ток проходить через электролит, состав которого обеспечивает протекание одной единственной реакции хотя бы на одном из электродов. Тогда, определив количество образовавшегося продукта реакции, мы можем, пользуясь величиной электрохимического эквивалента, точно рассчитать количество прошедшего электричества. Приборы, применяемые для этой цели, называются кулонометрами. [c.52]
Для стабилизации электролита по содержанию серной кислоты предложено вводить ее в виде соли трудно растворимого сернокислого стронция [1]. Избыток сернокислого стронция, находящийся в осадке, длительное время поддерживает требуемую концентрацию сернокислотного аниона в электролите. Состав электролита (г/л) хромовый ангидрид — 140—170 сернокислый стронций— 5—6. По данным работы [1], на рис. 9 приводятся сведения об интервале блестящих осадков, твердости, износостойкости и пористости покрытий, полученных из этого малоконцентрированного электролита. В табл. 1 приведены рекомендуемые режимы в зависимости от назначения покрытия. [c.12]
Применение анодно-струйного способа позволяет автоматизировать процесс хромирования и значительно повысить его производительность за счет более высокого выхода по току и применения высоких плотностей тока. При этом повышается равномерность отложения хромового покрытия по толщине слоя, создаются условия для получения осадков хрома заданной толщины. Установки для анодно-струйного хромирования могут быть созданы на несколько одновременно работающих ячеек. Вариантом анодно-струйной установки является анод, который не только подает электролит к хромируемой поверхности, но и равномерно отводит его из рабочего объема через ряд сливных отверстий на поверхности анода. Этим достигается большая равномерность омывания электролитом хромируемой поверхности, способствующая более равномерному осаждению покрытия, особенно при значительных плотностях тока. Этот вариант получил название возвратно-струйного хромирования [21]. Схема такого анода для хромирования коленчатого вала приведена на рис. 39. Ячейка состоит из двух половин, охватывающих шейку коленчатого вала. В корпусе установлен анод. Электролит подается через трубу в кольцевую канавку через осевые каналы — отверстия и поступает в рабочую зону. Удаляется электролит через систему отверстий и трубу отвода. Весь агрегат для возвратно струйного хромирования, использующего холодный электролит, состо нт из следующих узлов (рис. 40) электролитическая ячейка с анодом монтируемая на хромируемой детали, емкостей для электролита анодного травления и улавливания электролита, холодильный агрегат с теплообменным аппаратом, выпрямитель и система трубопрово дов с регулирующими клапанами. Ввиду особой важности под держания постоянного уровня электролита и температуры электроли та в заданных узких пределах рекомендуется оснастить ванну хроми рования устройством для автоматического регулирования уровня электролита и температуры [12]. [c.70]
Растворенная кислота НС1 переносится здесь из раствора раствор» не непосредственно, а в результате протекания двух противоположно направленных электрохимических реакций. Благодаря отсутствию диффузионных потенциалов такие цепи дают возможность точно определить коэффициент активности определенного компонента (в данном случае НС1 в электролите, состав которого можно усложнять). [c.547]
Кремнефтористоводородный электролит. Состав электролита и режим работы с ним следующие [c.27]
Растворимость анодных продуктов в электролите, скорость диффузии их в электролит, состав и физико-химические свойства анодной пленки имеют сушественное значение для процесса полирования. Поэтому этот процесс у различных материалов происходит неодинаково. У многих металлов и сплавов (медь, никель, алюминий, нержавеющие хромистые и хромоникелевые стали) сглаживание сопровождается появлением блеска на обработанной поверхности. У некоторых сплавов (стали карбидного класса, бронзы, латуни) наблюдается блеск без заметного сглаживания шероховатостей. Ряд металлов и сплавов (олово, свинец, серый чугун, высококремнистые стали) вовсе не полируется. Вместо сглаживания образуется сильно травленая поверхность с толстыми темными пленками. [c.111]
Выбор состава электролита и режима его эксплуатации зависит от назначения покрытия и вида подготовки. Так, при отсутствии операции амальгамирования первичное покрытие серебром производят в специальном электролите, состав которого приведен на стр. 36. [c.15]
Микроэлектрохимические измерения проводили в электролите, состав которого указан на с. 182. Для оценки влияния термической обр
www.chem21.info
кислотный, щелочной, корректирующий, состав и пропорции, как правильно приготовить и залить
Электролит – одна из основных составляющих аккумуляторных батарей, которые дают возможность запуска автомобиля. Он бывает нескольких видов, различающихся по своему составу. Своевременный контроль за количеством и качеством электролита в аккумуляторе позволит избежать преждевременный выход аккумулятора из строя и сэкономить на покупке нового устройства.
Виды, состав и особенности
На данный момент различают три вида электролитов для аккумуляторов, для щелочных аккумуляторов — щелочной, а для кислотных — кислотный, но так же выделяют и корректирующий электролит, необходимый при обслуживании батарей.
Как определить кислотный аккумулятор или щелочной? Проще всего это сделать по маркировке корпуса и по материалу, из которого он сделан. Корпус кислотных АКБ всегда изготавливается из специального пластика, тогда как щелочные батареи могут быть сделаны из металла. Так же можно определить протестировав каплю электролита из аккумулятора: кислотный электролит вступит в реакцию с содой или мелом.
Кислотный
Представляет собой смесь серной кислоты, составляющей тридцать пять процентов всего состава, и дистиллированной воды, которая занимает оставшиеся шестьдесят пять. Данный состав в аккумуляторе находится в емкости со свинцовыми пластинами, при контакте этих элементов и происходит выработка тока.
Преимущества кислотного электролита:
- Высокий уровень КПД
- Слабая потеря заряда при бездействии
- Выдача высокого стартового тока
- Невысокая стоимость
Недостатки:
- Чувствительность к перепадам температур
- Неэкологичность
- Необходимость регулярного контроля плотности состава
Следует отметить, что кислотный электролит используется в большинстве моделей аккумуляторных батарей для автомобилей, так как только он способен давать достаточное количество тока для запуска двигателя. При этом аккумуляторы, изготовленные с использованием данного раствора, делятся на две группы:
- Обслуживаемые
- Необслуживаемые
Первый вид обеспечивает легкий доступ к содержимому банок. В них можно замерять плотность электролита, при необходимости заливать дистиллированную воду и электролит, просто открутив крышки с банок.
В случае с необслуживаемыми моделями провести подобные действия также возможно, однако для этого нужно самостоятельно вскрыть устройство, провести нужные действия, а затем герметично их закрыть. В подобных случаях могут быть использованы дрель и сварочный аппарат.
Проводить замену электролита в необслуживаемых моделях стоит только в тех случаях, когда их гарантийный срок истек. Часто это производится исключительно для получения опыта проведения подобных операций.
Щелочной
Щелочной электролит состоит из гидроокиси калия, натрия, лития или всех этих составляющих в комплексе, разведенных в воде.
К достоинствам данного вида относятся:
- Длительный период службы
- Способность сохранять свойства при значительных перепадах температуры
- Гораздо меньшее выделение вредных газов в атмосферу
- Способность выдерживать встряски
- Неприхотливость в обслуживании
Недостатки:
- Меньшая величина электродвижущей силы по сравнению с кислотными
- Отсутствие способности подачи стартового тока для запуска двигателя
- Более высокая стоимость
Несмотря на долгий срок службы, неприхотливость и другие преимущества применение данного вида электролита в автомобильной промышленности ограничено. Виной тому неспособность выработки достаточного уровня стартового тока, необходимого для запуска двигателя. К минусам также относятся их внушительные габариты.
Однако устройства на щелочном электролите успешно применяются в обеспечении током тяговых и локомотивных составов.
Важно! Перед осуществлением замены следует убедиться, что аккумулятор именно щелочной. В противном случае АКБ можно полностью вывести из строя.
Корректирующий
Данный электролит является специальным составом с высоким содержанием активных веществ, используемый для повышения плотности электролита аккумулятора. Он предназначен для повышения концентрации активных веществ в батарее.
В продаже можно встретить следующие виды корректирующего электролита:
- Твердый калиево-литиевый
- Жидкий калиево-литиевый с различной плотностью
- Жидкий кислотный
Корректирующий электролит можно изготовить самостоятельно, имея под рукой необходимые для этого составы, однако зачастую его проще купить, так как стоимость его более чем доступна.
Как пользоваться корректирующим электролитом:
- Удалить из банок немного электролита
- Долить в них такое же количество корректирующей жидкости
- Установить АКБ на заряд номинальным током для запуска процесса смешивания полученного состава на полчаса
- Оставить батарею на остывание на пару часов
- Произвести замер плотности и при необходимости отрегулировать его снова
При повторной коррекции количество заменяемого электролита следует уменьшить.
Как приготовить самостоятельно
Перед тем, как самостоятельно заменить электролит для аккумулятора, необходимо принять соответствующие меры безопасности и приготовить предметы индивидуальной защиты:
- Перчатки
- Фартук
- Защитные очки
- Раствор соды на случай попадания средства на кожу или предметы одежды
- Уксус или лимонную кислоту – для нейтрализации щелочи
Проводить действия следует в хорошо проветриваемом помещении с температурой воздуха не выше +25 C°. Следует заранее знать, какой объем готового электролита потребуется для заполнения батарей. В среднем, в современных АКБ количество раствора составляет от 2,6 до 3,7 литра. Поэтому стоит сразу ориентироваться на максимальное количество. За основу можно взять 4 литра конечного раствора.
Для приготовления электролита необходимо заранее приготовить следующие предметы:
- Посуду достаточной емкости, изготовленную из материала, устойчивого к воздействию кислоты и щелочи
- Небольшую палочку для перемешивания электролита
- Инструменты для проведения замеров плотности, температуры и уровня раствора
- Для кислотного электролита – серную жидкость, для щелочного – щелочь в твердом или жидком виде, литий или силикагель
Важно! Все используемые материалы должны быть химически нейтральными для исключения возникновения ненужных реакций при их соприкосновении. В качестве емкости вполне подойдут обычные стеклянные банки.
Процесс приготовления щелочного электролита
Ингредиенты для приготовления данного состава могут быть как в жидком виде, так и в твердом. Если с первым все понятно, то перед тем как залить, щелочной электролит из твердого вещества потребуется развести в дистиллированной воде.
Требуемая плотность указывается на сайте производителя аккумулятора, также информацию можно найти в прилагаемой инструкции по эксплуатации. Твердый электролит берется пропорционально нужному количеству окончательного жидкого раствора и составляет:
- 1/5 – для получения раствора плотностью 1,17-1,19 г/м³
- 1/3 – для раствора плотностью 1,19-1,21 г/м³
- 1/2 — для раствора плотностью 1,25-1,27 г/м³
Процесс приготовления состоит из следующих шагов:
- Налить в посуду дистиллированную воду
- Добавить нужное количество щелочи
- Перемешать раствор
- Плотно закрыть крышкой
- Настаивать в течение 6 часов
После того, как процесс настаивания будет завершен, необходимо слить светлый раствор. Если часть состава выпадает в осадок, нужно его регулярно перемешивать. При заливке нужно следить, чтобы он остался на дне, не попав в аккумулятор, в противном случае это грозит выходом АКБ из строя.
Приготовление раствора для свинцовых аккумуляторов
Перед тем, как разбавить кислотный электролит, необходимо определить нужные пропорции. Они зависят от климатических условий, в которых планируется эксплуатация устройства.
Для получения электролита плотностью 1,28 г/м³, что приемлемо для средних климатических условий, потребуется в один литр дистиллированной воды влить 0,36 л серной кислоты. Для жарких регионов количество серной кислоты уменьшается до 0,33 л на то же количество воды.
Как разводить аккумуляторную кислоту:
- Налить в подготовленную емкость дистиллированную воду
- Аккуратно тонкой струйкой влить в нее кислоту
- Измерить плотность полученного раствора
- Оставить раствор настаиваться на 12 часов
Важно! Нельзя вливать воду в кислоту! Правильно — вливать кислоту в воду. Не следует торопиться, вливая кислоту, давайте возможность ей постепенно раствориться в воде.
Инструкция по замене
Замена электролита производится в следующих случаях:
- Электролит в банках изменил цвет, стал мутным. Причиной тому может быть использование не дистиллированной воды для добавки, а обычно. Она может содержать примеси, вступающие в химическую реакцию с электролитом и образовывая твердые соединения, выпадающие в осадок
- После зарядки аккумулятора невозможно добиться нужной плотности
- Электролит вытек по неосторожности
- Новый аккумулятор быстро разряжается. Причиной тому может быть замерзание раствора
Замена электролита, независимо от того, является он щелочным или кислотным, производится в несколько шагов:
- Демонтаж аккумулятора из транспортного средства
- Очистка АКБ от загрязнений
- Выкачивание имеющейся жидкости с помощью груши или шприца
- Промывка банок дистиллированной водой
- Заливка электролита с помощью груши или аналогичных приспособлений
Уровень заливки определяется метками внутри банок. Если они отсутствуют, нужно руководствоваться правилом – электролит должен быть на уровне выше пластин на 5-7 миллиметров. При этом от его уровня до крышек банок должно оставаться не менее двух сантиметров.
Очень важно при сливе электролита не наклонять его в сторону и тем более не переворачивать. На дне сосудов могут оказаться твердые частицы, которые застрянут в пластинах, полностью выведя их из строя. Допускается легкое покачивание воды из стороны в сторону при промывании, такие же действия можно производить после заливки электролита в аккумулятор.
После этого АКБ устанавливается на зарядку, после чего следует проверить получившуюся плотность. Замеры должны производиться не арене, чем через пару часов после снятия устройства с зарядки, так как существует риск получить завышенные показания. Если плотность недостаточно высокая или, напротив, имеет излишние значения, ее следует отрегулировать добавлением кислоты, щелочи или дистиллированной воды.
Полезное видео
Видео инструкция о замене электролита
Заключение
Независимо от типа электролита, используемого в эксплуатируемой АКБ, можно самостоятельно произвести его полную замену, проверку плотности и других показателей. Однако стоит помнить о технике безопасности, так как электролит – опасный химический состав, способный значительно повредить кожные покровы и глаза.
Вконтакте
Google+
akkummaster.com
Химический состав электролита
ВОЗОБНОВЛЯЕМЫЕ ИСТОЧНИКИ ЭНЕРГИИ
В качестве электролита может использоваться раствор щел или кислоты, расплавленный карбонат или твердый оксид.
Щелочные электролиты, например гидрооксид калия, используются обы в электролизерах (двойник топливного элемента — вместо производства эле рической энергии за счет потребления топлива они производят топливо за потребления электроэнергии). Использования щелочи в топливных элеме стараются избегать, так как присутствие в воздухе (который используется в честве окислителя) углекислого газа приводит к образованию нераствори карбонатов, которые ухудшают свойства электролита. Лишь в особых случ когда окислителем является чистый кислород, топливные элементы с электро. том КОН демонстрируют высокую эффективность. Такие топливные элеме используются в космической отрасли.
Растворы кислот имеют более высокую коррозионную активность, чем лочи, однако относительно слабые кислоты могут достаточно эффективно пользоваться в топливных элементах. В частности, широкое применение и фосфорная кислота1). Она устойчива к диоксиду углерода. Для эффективной боты необходимо поддерживать температуру электролита в диапазоне от 150 220 °С. При этом давление в системе должно быть повышено, чтобы жидко, не закипела. При более низких температурах электрическая проводимость твора слишком мала, а при более высоких возникают проблемы с прочное используемых материалов. Предлагается также использовать твердые кисло качестве электролита для топливных элементов (см. п. 7.5.7). Их использова может помочь в решении неприятной проблемы, связанной с просачиван метанола через мембрану от анода к катоду (см. п. 7.5.6).
Большая часть твердооксидных электролитов, таких как стабилизирован цирконий и диоксид церия, обладают анионной проводимостью, т. е. явля проводниками для отрицательных ионов, например О2-. Существуют и пре жены для использования и электролиты с катионной проводимостью.
Твердополимерный электролит, как правило, является проводником прото как и кислоты. Однако, как и в случае твердооксидных электролитов, разр тываются и исследуются также и твердополимерные электролиты с катион проводимостью.
‘* Фосфорная кислота довольно слабая, что подтверждается ее ежедневным потреблением бителей напитка кока-кола, в состав которого она входит.
7.3. ХИМИЧЕСКИЕ РЕАКЦИИ, ПРОТЕКАЮЩИЕ
В ТОПЛИВНОМ ЭЛЕМЕНТЕ
Тип химических реакций, протекающих в топливном элементе, ;ісит как от вида используемого топлива, так и от типа электролита. Некото — е из наиболее распространенных комбинаций описаны ниже и показаны на люстрациях (см. с. 278).
7.4.1. Щелочные электролиты
В водородно-кислородных топливных элементах с щелочным ектролитом (обычно КОН) токообразующим является ион ОН. Так как ион держит атом кислорода, на аноде образуется вода.
Диссоциация КОН в электролите описывается уравнением:
КОН ^ К+ + ОН’ • (8)
На аноде нейтральные атомы водорода соединяются с гидроксильными ио — ми, в результате чего образуются молекулы воды и электроны, образующие во внешней цепи:
2Н2 + 40Н — -> 4Н20 + 4е» . (9)
На катоде электроны снова образуют ионы гидроксила:
4е~ + 02 + 2НгО -> 40Н — . (10)
Электролит в этих реакциях, разумеется, не расходуется. Общее уравнение
лЦИИ
2Н2+02^2Н20. (11)
РАБОТА
Выше мы говорили о том, что газ, находящийся в цилиндрическом сосуде с поршнем, может совершать работу. Какова эта работа? Сила, действующая на поршень со стороны газа, равна рА, где А …
ПЕРВЫЙ ЗАКОН ТЕРМОДИНАМИКИ
Подведем некоторое количество Q теплоты к газу, находящему- ■ : цилиндре с адиабатическими стенками и поршнем внутри, который может ■сремещаться без трения. Наличие адиабатических стенок означает, что тепло — р …
УДЕЛЬНАЯ ТЕПЛОЕМКОСТЬ ПРИ ПОСТОЯННОМ ОБЪЕМЕ
При изменении температуры некоторого фиксированного количества газа будет меняться его внутренняя энергия. Если при этом объем газа остается постоянным (например, газ помещен в сосуд с жесткими стенками), то изменение его …
msd.com.ua
Состав электролита
Глинозем и криолит являются основными составляющими электролита при производстве алюминия электролизом. Многочисленные попытки заменить криолит другими расплавленными средами не привели к положительным результатам. Преимущества криолита заключаются в хорошей растворимости в нем глинозема и отсутствии элементов с более положительным потенциалом, чем алюминий, которые, разряжаясь на катоде могли бы загрязнять металл. Криолит-глиноземные расплавы характеризуются достаточной электропроводимостью, сравнительно небольшим давлением насыщенного пара. Плотность электролита меньше плотности расплавленного алюминия, что позволяет применять в качестве катода алюминий, располагаемый под слоем электролита.
Все физико-химические свойства электролита существенно зависят от содержания Al2O3, которое изменяется в процессе электролиза. По мере уменьшения содержанияAl2O3 растут температура начала кристаллизации, плотность и электропроводность электролита, уменьшается его вязкость.
Конструкция и эксплуатация электролизеров
Современный электролизер состоит из пяти основных частей: корпуса ванны, катода, анода, катодного токоподвода и анодного токоподвода (рис. 15.1)
Рис. 15.1. Электролизер с самообжигающимися анодами: 1 – чугунная заливка; 2 – шамотный кирпич; 3 – стержень; 4 – угольные блоки; 5 – гарниссаж; 6 – угольные плиты; 7 – серьга; 8 – гибкие шины; 9 – анод; 10 – стойка для анода; 11 – ребро жесткости; 12 – рама анода; 13 – жидкая масса; 14 – тестообразная масса; 15 – медная шина; 16 – штырь.
Корпус ванны изготавливают из стальных листов, футеруют угольными блоками 4 и плитами 6.
В работающей ванне образуется корка застывшего электролита – гарниссаж 5, которая предохраняет футеровку от разрушения расплавленным электролитом.
Катодом служит расплавленный алюминий, который расположен на дне электролизера в виде слоя высотой 0,1 – 0,2 м. Подвод тока к расплавленному алюминию через угольные блоки 4 осуществляется с помощью стержней 3. Введенные в блоки стальные стержни для улучшения контакта заливают чугуном или утрамбовывают углеродистой массой.
В качестве анодов в электролизерах применяются угольные блоки 4. Многоанодные электролизеры на большинстве заводов теперь заменены одноэлектродными, что значительно упростило регулирование работы электролизеров.
Аноды подвешивают на железную раму 12 с помощью стальных штырей 16, которые одновременно служат для подвода тока. На углах анодной рамы закреплены тяги, соединенный с подъемным механизмом. С помощью подъемного механизма анод по мере его сгорания можно опускать вниз.
В современных электролизных цехах ванны расположены в два или четыре ряда. В связи с применением электролизеров большой мощности предлагают располагать ванны в один ряд в двухэтажном здании. Число последовательно соединенных в серии алюминиевых ванн может достигать 160.
С увеличением мощности агрегатов снижаются удельные капитальные вложения, повышается производительность труда, но с увеличением токовой нагрузки возрастает и отрицательное влияние электромагнитных и гидродинамических сил. С повышением мощности ванн удельные капитальные затраты и себестоимость алюминия достигают минимальных значений в интервале 150 – 175 кА при ширине анода в 3 м.
В настоящее время свыше 80% цеховых затрат приходится на долю сырья, основных материалов и электроэнергии.
studfiles.net