Как производится ремонт шлангов высокого давления и какие есть нюансы
Содержание статьи
Шланги высокого давления, чаще называемые рукавами высокого давления (РВД), предназначены для создания или поглощения рабочего усилия, которое под высоким давлением передается закачанными в них жидкостями или газами.
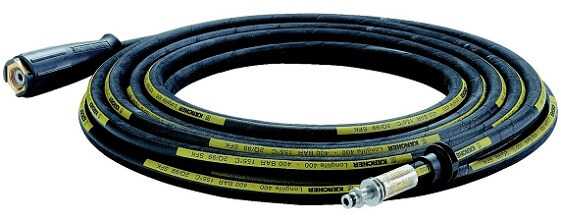
Шланг высокого давления
Основная область применения РВД – гидравлические и пневматические системы различных устройств и механизмов. Вне промышленного производства с РВД чаще всего имеют дело владельцы автотранспорта, это шланги гидроусилителя руля (ГУР), и те, кто пользуются насосами высокого давления, например, самой распространенной у нас марки Керхер.
Вернуться к содержанию ↑Структура РВД
Конструкция РВД обусловлена необходимостью выдерживать внутреннее давление, которое может доходить до нескольких сотен атмосфер.
Кроме того, внутренняя поверхность шланга высокого давления должна быть невосприимчива к воздействию транспортируемой среды. Поэтому нижний его слой делается из маслобензостойкой резины или синтетического каучука.
Для изготовления верхнего, более толстого слоя рукава высокого давления используется износостойкая резина, которая в случае необходимости дополняется термозащитой в виде гофрированного покрытия, металлического или полимерного.
Между верхним и нижним слоями резины в несколько слоев наматывается металлическая проволока, благодаря чему шланг получает нужную жесткость и прочность. Слои проволоки перемежаются тонкими резиновыми плёнками.
В зависимости от способа намотки проволоки различаются два вида шлангов высокого давления:
- Навивочные. При производстве шлангов этого типа витки проволоки наматываются ровными рядами.
- Оплеточные. В этом случае витки навиваются под углом к оси шланга так, чтобы витки предыдущего слоя скрещивались с витками следующего слоя проволоки. Оплеточные РВД обладают большей прочностью и способны выдержать большее давление, чем навивочные шланги.
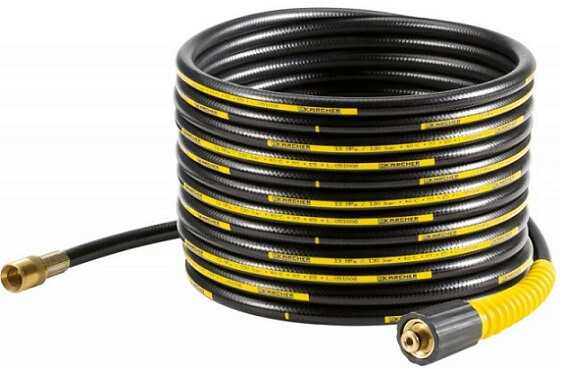
Рукав высокого давления
В роли внутреннего жесткого каркаса кроме проволоки может выступать текстиль.
Количество слоёв проволоки и толщина слоев резины задаются стандартами, определяющими область применения того или иного типа РВД.
Вернуться к содержанию ↑Фитинги для РВД
Для крепления шлангов по месту на их концах монтируются фитинги (наконечники), которые бывают следующих типов:
- Гайка;
- Штуцер;
- Ниппель;
- Быстроразъемные соединения.
Крепление фитингов к концам шланга производится с помощью обжимных муфт, которые опрессовываются на специальных станках.
В зависимости от вида хвостовика фитинги классифицируются по сериям:
- Универсальная. Эта серия может применяться во всех шлангах РВД за исключением шлангов навивочного типа.
- Interlock. Серия используется для навивочных рукавов.
- CS. Фитингами этой серии так же обжимаются навивочные рукава, но снимать резину верхнего и нижнего слоя при этом уже не надо.
При установке фитингов этого типа требуется обязательно удалять оба слоя резины, внутренний и внешний.
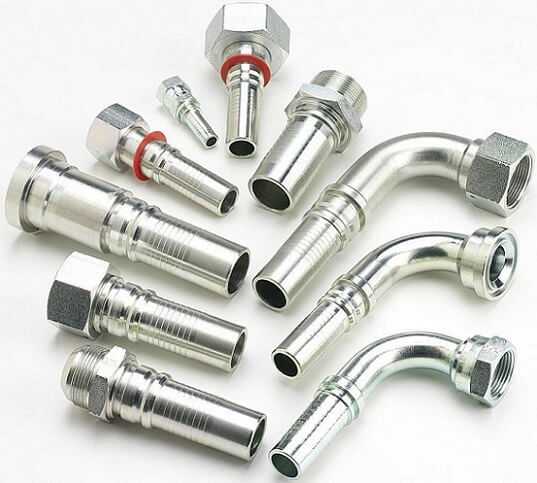
Фитинги для рукавов высокого давления
Операция по удалению слоев резины называется окорка шланга.
Выход из строя фитингов является наиболее частым случаем повреждения шлангов высокого давления. Это объясняется величиной и интенсивностью испытываемых ими нагрузок.
Вернуться к содержанию ↑Повреждения шлангов высокого давления
Причины повреждений можно разделить на следующие виды:
- Заводской брак. Чаще всего это некачественный обжим стыка фитинга со шлангом, вследствие использования кустарного или неотлаженного оборудования.
- Повреждения, полученные при работе основного механизма. Они проявляются в виде порезов и разрывов шланга. Наиболее распространенной их причиной является провисание РВД из-за неправильно подобранной длины.
- Повреждения, полученные из-за несоответствия параметров РВД условиям эксплуатации. Это может быть разрыв шланга или срыв фитинга, из-за этого давление оказалось выше того, на которое рассчитан рукав.
- В этом же ряду следует назвать повреждения внешнего слоя РВД при использовании его не в том температурном режиме, на который он рассчитан.
Важно! Чтобы максимально обезопаситься от возможных повреждений РВД, при их выборе необходимо тщательно проверять соответствие их характеристик и параметров условиям эксплуатации.
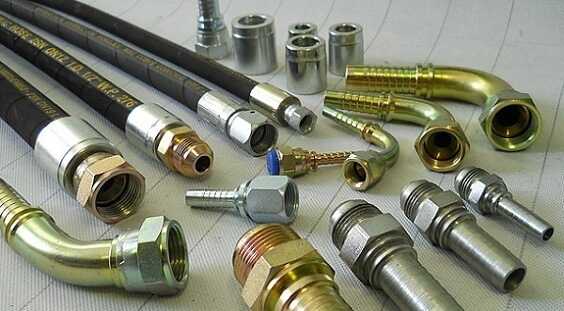
Рукава высокого давления с фитингами
Речь идет, прежде всего, о расчетном значении максимально допустимого значения давления, температуры и минимальном радиусе изгиба рукава.
Среди повреждений шлангов высокого давления наиболее распространенными являются следующие:
- Поражение коррозией фитингов.
- Излом рукава.
- Истирание и изношенность верхнего слоя шланга.
- Закупорка рукава.
- Нарушение герметичности соединения фитинга.
- Срыв фитинга со шланга.
- Протечка соединения фитинга.
- Термическое повреждение внутреннего слоя резины.
Замена поврежденных шлангов высокого давления
Из всего вышесказанного можно сделать вывод, что ремонт РВД заключается или в замене поврежденного участка или в замене пришедших в негодность фитингов.
При замене поврежденного участка, так же как и при замене фитингов, понадобится обжимать соединительные муфты, то есть технологически эти два действия очень похожи.
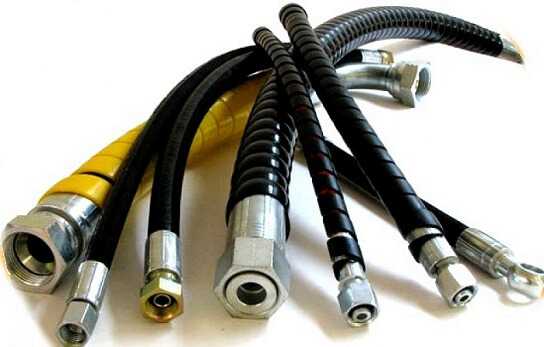
Шланги высокого давления
Последовательность операций при этом выглядит таким образом:
- Поврежденный рукав отсоединяется от основного механизма.
- На отрезном станке режется новый рукав по размеру старого. Причем для замера берется расстояние между торцами ниппелей на его концах. Выбирать лучше РВД, рассчитанный на большее давление, чем то, на которое был рассчитан старый РВД.
- Подобрать нужный диаметр поможет маркировка, которая ставится на рукавах.
- Если предстоит ремонт рукава, рассчитанного на повышенное давление (тяжелого рукава), его концы зачищают изнутри и снаружи до металлической оплетки. Эта операция производится на окорочных станках.
- Затем подбирают нужные фитинги. Это может быть сопряжено с определенными сложностями, так как импортные фитинги изготовляются по разным стандартам.
В случае затруднений проще всего произвести замеры по старому фитингу штангенциркулем и резьбомером, что позволит точно установить нужные диаметр и шаг резьбы и затем подобрать нужные параметры нового фитинга по таблицам. - После окорки и подбора фитингов производится их опрессовка на обжимных станках. Для каждого диаметра подбираются съемные обжимные кулачки.
- Далее обязательно проводится проверка качества опрессовки. Для этого используется контрольный щуп, но лучше всего проводить тестирование на специальном испытательном стенде.
Заводская маркировка DN обозначает диаметр внутреннего канала шланга.
Если попалось нестандартное соединение, то ремонт осуществляется с помощью ремонтного фитинга. Для этого берется головка старого фитинга, к которой припаивается часть, подлежащая опрессовке.
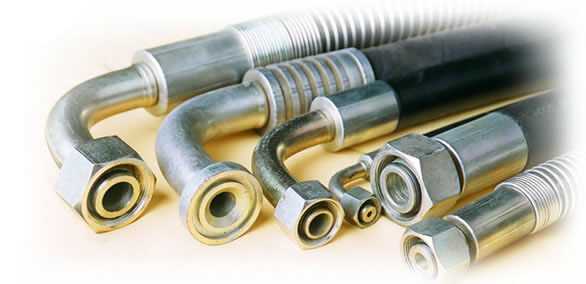
Рукава высокого давления
Этим методом часто пользуются автолюбители для экстренного ремонта шлангов ГУР, а так же владельцы насосов и минимоек Кирхер.
Вернуться к содержанию ↑Ремонт и замена шлангов ГУР
Причина возникновения повреждений шлангов ГУР чаще всего состоит в том, что при вращении рулевого колеса в силу трения возникает серьезное усилие. Это усилие вызывает деформацию эластичного элемента, который меняет размеры отверстий в распределительном механизме, регулирующем перепад давления в гидроцилиндре.
В результате изнашивается рукав ГУР, подведенный к ограничительному клапану. Этот рукав ГУР рассчитан на давление, в зависимости от марки автомобиля, от 70 до 130 кГс/см2.
При таком высоком давлении ремонт поврежденного шланга ГУР с помощью хомутов или проволоки практически невозможен.
Остается два варианта: или заменить трубку ГУР целиком, или заменить только поврежденную её часть, переставив фитинги на новый шланг.
Причем перестановку фитингов лучше производить в условиях специальной мастерской.
Замена и установка шланга ГУР производится следующим образом:
- Передняя часть автомобиля поднимается на домкратах.
- Руль до упора выворачивается влево.
- Шприцем с насаженной на иголку трубкой из бачка гидроусилителя откачивается жидкость.
- После этого отсоединяется шланг, рабочие отверстия гидравлической системы закрываются заглушками.
- Затем производится установка нового шланга, заливка жидкости в гидравлическую систему и проверка качества монтажа.
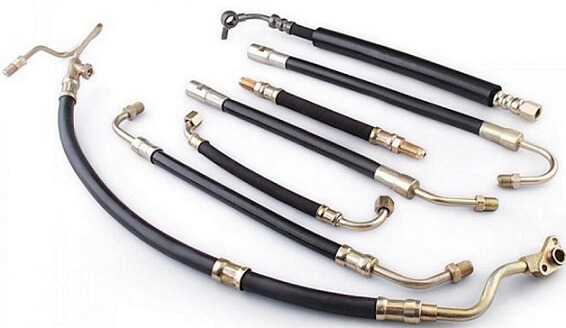
Шланги гидроусилителя руля
Подбор нового шланга производится с точным соблюдением диаметра, иначе могут измениться рабочие качества гидроусилителя.
Заключение
Люди, обладающие профессиональными навыками, способны отремонтировать РВД для гидравлических систем автомобиля или насоса Керхер вручную, используя простейшее оборудование и приспособления. Но качество такого ремонта останется под сомнением, что крайне не желательно.
Надо понимать, что высокое давление создает зону повышенного риска, когда поломка или нештатное функционирование РВД может привести к тяжелым последствиям. Особенно, когда это касается не насоса Керхер, а гидравлических систем тяжелой техники. Далеко не полный список таких последствий выглядит так:
- Отстрел фитингов и опасный выхлест сорванных шлангов;
- Возгорание или взрыв рабочей жидкости;
- Потеря управляемости автомобилем;
- Отравления и ожоги из-за вылившейся из шлангов жидкости.
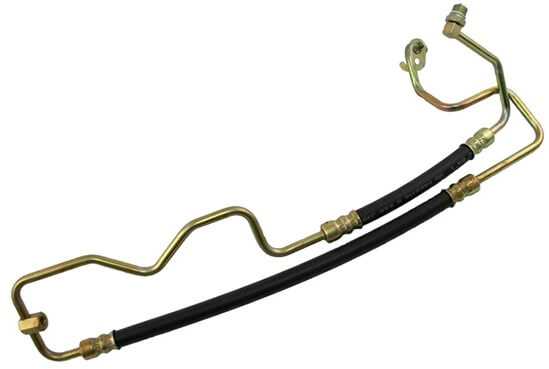
Шланг ГУР
Избежать этого и обеспечить продолжительную и качественную работу отремонтированного трубопровода поможет точное соблюдение инструкций, внимательность и аккуратность при монтажных работах, а так же обращение в случае необходимости к специалистам.
Вернуться к содержанию ↑Штуцер для ремонта шлангов высокого и низкого давления
Автор | Поделитесь | Оцените | Виктор Самолин |
---|
vseotrubax.com
Как обжать шланг высокого давления своими руками?
Вообще правильно обжимают шланги высокого давления при помощи вот таких фитингов (арматура, прессуемая, шланговая, полное название)
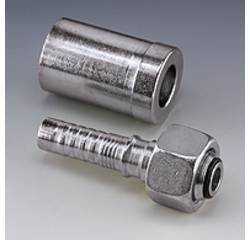
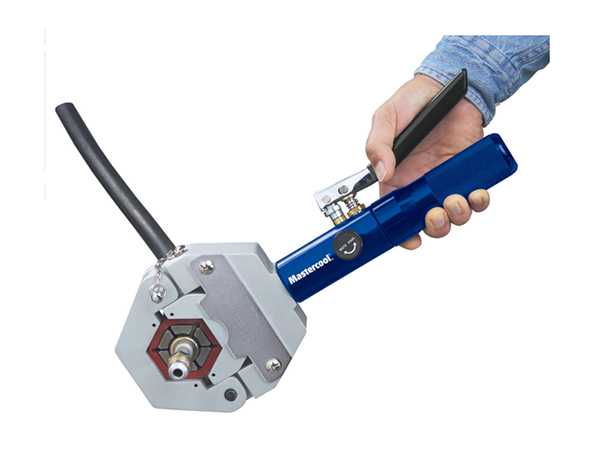
Одеваем втулку на шланг, вставляем фитинг, далее всю конструкцию помещаем в «кулачки» станка и обжимаем.
Вот именно эти действия считаются правильными.
Если хотите нечто «самопальное» и нет станка для обжима шлангов, то можно сделать следующее (так некоторые умельцы ремонтируют шланги высокого давления Керхер).
Покупаем вот такие фитинги «ёлочка»
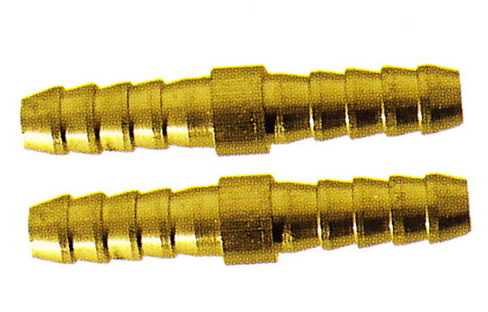
Диаметр (наружный) «ёлочки» в соответствии с внутренним диаметром шланга, «ёлочка» должна входить очень плотно.
Далее вот таки хомуты с планкой и гайками,
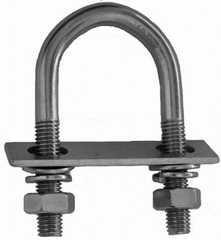
Смазываем «ёлочку» (предварительно один конец зажав в тисках).
Двумя руками вставляем один конец шланга в фитинг (двумя потому что сам фитинг очень плотно входит в шланг, это основа всего мероприятия).
Одеваем первый В-образный хомут и затягиваем гайки.
Всё тоже самое со вторым концом шланга, одеваем второй хомут и затягиваем.
Хомуты могут сползти, давление высокое, связываем их между собой сталистой проволокой, скручиваем.
Вот и всё на финише весь этот «самопал» можно обмотать фольгированным скотчем.
Не раз видел такую «залипуху» на авто-мойках, всё работает, причём длительное время.
www.remotvet.ru
Ремонт гидрошлангов и РВД
Услуги >> Ремонт гидрошлангов и РВД
____________________________________________________________________________________________
Ремонт гидрошлангов и РВД – экономия Своих денег и времени.
В отечественных условиях, с одной стороны, — парк автомобильной, специальной и другой техники и оборудования очень разнообразен
В такой ситуации, ремонт вышедших из строя элементов гидравлических систе (в том числе, гидрошлангов и РВД), из-за их отсутствия, заканчивается «народными» средствами. Взамен родному изделию, пытаются приспосабливать попавшиеся под руку «похожие» гидравлические шланги.
Заказать новый? Во-первых, часто изделие уже не выпускается, во-вторых, — сроки ожидания заказа порой, более месяца, в-третьих, — необоснованная цена,
Экономия при ремонте гидравлических шлангов и РВД достигает до 70% от цены нового изделия.
А сколько примеров, когда после самостоятельного обслуживания или ремонта гидравлических узлов и изделий, люди делились впечатлениями: «..а оно, вдруг, как треснет…», «…мы думали, а там уплотнение, оказывается, было…», «… чуть посильнее надавил, — лопнуло» и т.д.
И дело здесь не в «прямых» руках, обычно, это мастеровые люди (как в пословице: кто не работает, тот не ошибается). Просто,
Поэтому, чтобы не «изобретать велосипед», сделать ремонт профессионально, быстро и не переплатить, мы предлагаем простое решение, — за профессиональным ремонтом специальных элементов, а гидравлические шланги (РВД) к ним и относятся, обращайтесь в HYDRO-BOSS «Гидро-Босс»
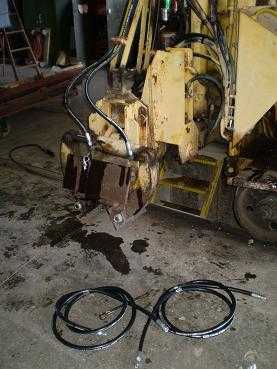
Мастерская «Гидро-Босс», — это специализированный сервис по ремонту гидравлических шлангов (рукавов) РВД.
Если же Вы хотите организовать самостоятельный ремонт гидрошлангов и РВД, мы готовы Вам предложить как отдельно обжимное оборудование: Оборудование для производства РВД >>, так и Комплекты оборудования для РВД >>
Сберегите Ваше время и останетесь при Своих деньгах.
Свяжитесь с нами Сегодня: Контакты >>
Ремонт гидросистем, а также их составные части.
Тема №4: Ремонт гидросистем, а также их составные части.
Составить отчет:
1.Основные не исправности и причины возникновения.
2.Ремонт, устранения не исправностей и основные регулировки.
3.Создать инструктивную карту на восстановление (узла, детали)
РЕМОНТ ОСНОВНЫЕ НЕИСПРАВНОСТИ ГИДРАВЛИЧЕСКОЙ СИСТЕМЫ
Шестеренчатый насос. Износ стенок и дна колодцев корпуса, торцов шестерен и поверхностей цапф, отверстий втулок под цапфу, откалывание кромок буртиков крышки насоса под уплотнительный сальник, износ плоскости крышки.
Распределитель. Трещины корпуса и крышки, износ золотников, износ конусной поверхности перепускного клапана, кромок его гнезда, зазор между осью и рычагом верхней крышки свыше допустимого, износ хромового покрытия рычага, золотников и отверстий под золотники в корпусе, срыв резьбы в отверстиях корпуса.
Цилиндр. Износ стенок гильзы, поверхностей поршней и штоков. Износ отверстий передней крышки, соединительных отверстий в крышках и вилках штока. Износ и повреждения уплотнительных резиновых колец, износ или срыв резьбы штока.
Гидроусилитель рулевого управления тракторами МТЗ-50, МТЗ-50Л, МТЗ-52, МТЗ-52Л, МТЗ-80, МТЗ-80Л, МТЗ-82 и МТЗ-82Л. Износ рабочей поверхности упора, износ и повреждения рейки, износ отверстий рейки под палец, гильзы цилиндра, поршня штока, износ шеек и изгиб поворотного вала, износ отверстий корпуса под золотник и золотников.
Запорное устройство и разрывная муфта. Нарушение герметичности клапанов, износ и повреждения резьбовых соединений, дефекты крестовин и пружин.
Баки и фильтры. Трещины сварных соединений и пробоины стенок баков, нарушение герметичности, износ клапанов, повреждения деталей фильтра.
Шланги. Нарушение герметичности заделки и разрывы шлангов, повреждения резиновых слоев.
РЕМОНТ АГРЕГАТОВ ГИДРАВЛИЧЕСКОЙ СИСТЕМЫ
Шестеренчатый насос разбирают и ремонтируют, если у него объемный к. п. д. менее 0,6 (после замены уплотнений). Чтобы правильно контролировать этот показатель, необходимо различать обозначения гидравлических насосов. В маркировках НШ-10Д, НШ-32 (НШ-32Э) и НШ-46У цифра соответствует теоретической производительности нового насоса в кубических сантиметрах за один оборот шестерен. Буквы Д, Э, У после цифры означают модель насоса. Направление вращения ведущей шестерни показано на табличке насоса буквой Л (левое) или П (правое).
Размеры корпуса гидравлического насоса, мм
Марка насоса |
Маркировка |
Д |
Д1 |
|
d1 |
d2 |
А |
Н |
Н1 |
НШ-10 |
Новый |
— |
69 |
||||||
Р1 |
— |
0,02 |
69 |
||||||
Р2 |
— |
69 |
|||||||
Р3 |
— |
69 |
Размеры для корпусов, восстановленных обжатием.
При разборке насосов отвертывают болты, снимают крьшжу насоса и вынимают детали вручную. Съемник применяют только при снятии из гнезда нижней пары втулок. Втулки, крышки и уплотнительные кольца насосов НШ-32 и НШ-46 взаимозаменяемы, но если насос собирают снова из этих деталей, то обезличивание втулок и шестерен не допускается.
Поступившие первый раз в ремонт насосы ремонтируют методом смещения шестерен концентричными втулками. Этот способ позволяет отремонтировать насос с меньшими затратами, так как восстановление корпуса насоса сводится к одной операции — расточке колодцев на увеличенный размер (табл. 30, рис.37). Насос собирают с эксцентриковыми втулками, величина смещения оси шестерен должна быть равна половине разности размеров головок зубьев шестерен и колодцев корпуса.
Запорное устройство испытывают на стенде для испытания гидроагрегатов при давлении масла 8,0—10,0 МПа. При таком давлении течи масла в сопряжении шарик — корпус не должно быть.
Разрывная муфта отличается от запорного устройства тем, что вместо накидной гайки применяется специальный замок.
Баки с фильтрами. Для испытания клапанов фильтров используют приспособление, которое присоединяют к штуцеру стенда К. К-4200 с насосом НШ-32. На приспособлении устанавливают манометр низкого давления со шкалой 0,4—1,0 МПа.
Предохранительный клапан фильтра не должен пропускать масло при давлении 0,15 МПа. При давлении 0,25—0,35 МПа клапан должен пропускать все количество масла, подаваемого насосом.
Шланги гидравлической системы состоят из рукавов и наконечников, при помощи которых их присоединяют к штуцерам маслопроводов и гидроагрегатов.
Шланги оборудованы наконечниками неразборной конструкции. Наиболее частыми дефектами шлангов являются разрывы в местах подсоединения рукавов к наконечникам. В этих случаях поврежденную часть обрезают дисковым ножом (рис. 57, а) или наждачным кругом, на отрезанном конце устанавливают исправный наконечник.
Ниппеля и гайки выбракованных наконечников вновь используют. Для этого подрезают кромку буртика муфты Ниппель с гайкой извлекают из шланга при помощи приспособления затем также, используя приспособление, вставляют их внутрь годного конца шланга предварительно установив муфту.
Перед установкой муфты срезают наружный резиновый слой на длине 40—41 мм. Армированный шланг обжимают штампом под прессом мощностью 1 МП. Для обжатия различных по диаметру шлангов в штампе предусмотрены сменные кулачки 4
Если длина годного конца шланга недостаточна для использования, то обрезанные концы шланга соединяют при помощи двойного ниппеля (см. рис. 58). Наружный резиновый слой удаляют с концов соединяемых шлангов на длине 40 мм и надевают втулку длиной 92 мм и толщиной стенки 1,5—2 мм. Смазав двойной ниппель солидолом, вставляют его в концы шланга и обжимают в штампе. Ниппель можно обжимать в патроне токарного станка или труборезом, в котором кольцевые ножи заменены тремя калеными роликами диаметром 35 мм и шириной-8 мм.
Разборная заделка шлангов высокого давления показана на рисунке 60. Чтобы армировать шланг, обрезают его поврежденную часть, снимают наружный 1 резиновый слой до металлической оплетки 2 на длине 40 мм от конца шланга и вырезают внутренний 3 слой резины на глубину 10 мм. На подготовленный конец шланга надевают муфту 4, а большой ниппель 6 вставляют в шланг. Чтобы концы металлической оплетки равномерно расположились на конусной части большого ниппеля, металлическую оплетку слегка расплетают. Гайкой 5 прочно затягивают металлическую оплетку между муфтой и большим ниппелем. Установив накидную гайку 8 на малый ниппель 7, завертывают его. в большой ниппель. Малый ниппель после установки на него гаек 5 и 8 приваривают газовой сваркой к большому ниппелю, чтобы создать герметичность соединения.
Гидроувеличитель сцепного веса (ГСВ). Изношенные ползун, золотник и отверстия в корпусе восстанавливают т. еми же способами, которые применяют при ремонте золотниковых пар распределителей Р75-ВЗ.
Гидроувеличитель сцепного веса испытывают на стенде КИ-4200. При испытании сначала проверяют герметичность, а затем работу ГСВ.
При проверке герметичности ГСВ присоединяют к стенду по схеме, показанной на рисунке 61.
Испытание проводят в следующем порядке:
а) для проверки герметичности запорного клапана рукоятку ГСВ устанавливают в положение «заперто», а на нагнетательный и сливной штуцера ГСВ навертывают заглушки (рис. 61, а). Включают электродвигатель стенда и устанавливают дросселем давление
Схема испытания гидроувеличителя сцепного веса и гидроаккумулятора на стенде КИ-4200:1-насос 2-гидроаккумулятор; 3-гидроувеличитель сцепного веса; 4 — дроссель-расходомер; 5 — тройник.
по манометру стенда до 6,0—7,0 МПа. При этом величина утечки масла через штуцер для подключения гидравлического аккумулятора не должна превышать 6 см3 за 10 мин. По окончании проверки открывают дроссель и выключают электродвигатель стенда;
б) для проверки герметичности ползуна рукоятку ГСВ устанавливают в положение
«выключен» (рис. 61, б). Затем включают электродвигатель стенда и устанавливают дросселем давление по манометру стенда до 6,0—7,0 МПа. При этом величина утечки масла
через штуцер для подключения гидравлического аккумулятора не должна, превышать
50 см3 за 10 мин.
Перекрывая дроссель стенда, устанавливают давление по манометру стенда до 10,0 МПа и проверяют герметичность ГСВ в течение 1 мин.
При этом давлении, а также в процессе других испытаний просачивание масла в местах соединений не допускается.
По окончании проверки открывают дроссель и выключают электродвигатель стенда;
в) для проверки герметичности и давления срабатывания предохранительного клапана рукоятку ГСВ устанавливают в положение «включен» (рис. 61, в). Заглушку переставляют со сливного штуцера на штуцер для гидравлического аккумулятора. Включаютэлектродвигатель стенда и при помощи дросселя повышают давление до срабатывания
клапана, которое определяется по вытеканию струи масла из сливного штуцера. Срабатывание клапана должно быть четким. Подтекание масла до срабатывания клапана свидетельствует о его негерметичности.
Распределительный кран:
1-кран; 2-шпилька; 3-болт; 4-пружинная шайба;5-грязесъемная манжета; 6 и 7-уплотнителыше кольца;8-верхняя крышка;9 и 11-штуцера; 10 — прокладка; 12- корпус; 13- нижняя крышка.
Давление срабатывания клапана проверяют как при отвернутом, так и при завернутом маховичке ГСВ. Оно должно быть на 0,8—2,0 МПа выше давления зарядки гидравлического аккумулятора.
Работу ГСВ и гидравлического аккумулятора проверяют по схеме.
Перед испытанием, вращая маховичок ГСВ по часовой стрелке, устанавливают его в крайнее положение и, вращая иглу приспособления, перекрывают сливное отверстие. Рукоятку ГСВ устанавливают в положение «включен». Включают электродвигатель стенда и, перекрывая дроссель стенда, наблюдают за манометрами стенда и дросселя-расходомера. Манометр стенда будет показывать давление только при зарядке гидравлического аккумулятора. Манометр дросселя-расходомера — давление в гидравлическом аккумуляторе (давление подпора).
Для проверки работы автоматического регулятора вращают маховичок ГСВ против часовой стрелки. из одного крайнего положения в другое. При этом давление подпора, определяемое по манометру дросселя-расходомера, должно изменяться от 0,8 МПа до 2,8| МПа скачками. Количество скачков должно быть 3—4, учитывая скачок первоначальной зарядки гидравлического аккумулятора. Проверку повторяют 2—3 раза, разряжая гидравлический аккумулятор отвертыванием иглы дросселя-расходомера и выпуская масло.
Гидравлический аккумулятор тракторов МТЗ-50, МТЗ-50Л, МТЗ-52, МТЗ-52Л. Гидравлический аккумулятор испытывают на стенде КИ-4200, навернув на его штуцер дроссель-расходомер для проверки и присоединив его к нагнетательной линии стенда. При давлении 6,0 МПа течи масла по разъемным плоскостям, а также из отверстия, закрываемого пробкой, в течение 3 мин не должно быть.
Плавность работы проверяют при постепенной разрядке гидроаккумулятора, находящегося под давлением 4,0—6,0 МПа. При этом давление в диапазоне от 3,1 до 0,8 МПа должно падать плавно, без скачков.
Распределительный кран. Промыв детали в дизельном топливе, собирают нижнюю крышку 13 вставив в ее кольцевую расточку резиновое уплотнительное кольцо 7.
Рис. 37. Корпус гидравлического насоса.
mehanik-ua.ru
Ремонт гидравлики и гидравлических систем в Москве
Ремонт гидравлики: гидроцилиндров, гидронасосов и другого гидрооборудования. Сжатые сроки, качественный ремонт и длительная гарантия на предприятии ООО «Гидротехтрейд».Наша компания имеет успешный многолетний опыт оказания высококачественных услуг в сфере ремонта гидравлического оборудования в Москве и по всей России. У нас есть все необходимое для решения самых сложных задач. Специализируемся на ремонте гидравлических систем импортного производства. Ждем ваших звонков, Уважаемые клиенты! (495) 660-0423
Ремонт гидравлических цилиндров дополнительно включает в себя возможность восстановления изношенных поверхностей гильз и штоков гидроцилиндров.
Наша компания также производит диагностику гидравлики у себя или на территории заказчика.
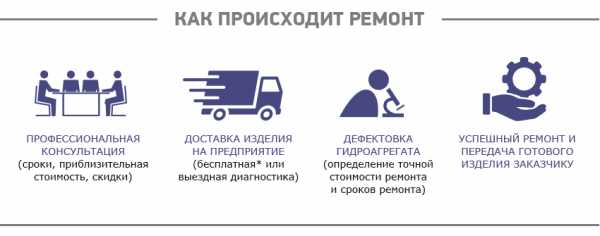
Рассчитать
На предприятии ремонтируют разную гидравлику, для:
И др. оборудования…
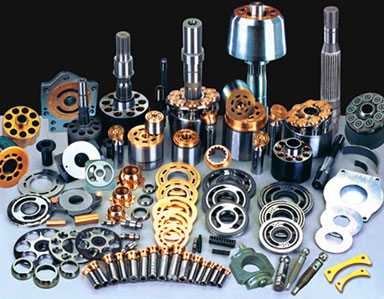
Обращаем Ваше внимание, мы не ремонтируем:
- раздутые корпуса для гидронасосов и гидромоторов;
- нарушенную геометрию гильз и штоков гидроцилиндров (разрыв, вздутие, трещина).
Порядок проведения работ по ремонту:
Перед началом работы наш менеджер производит полную консультацию по телефону и помогает клиенту определить приблизительную стоимость и сроки работ, а так же целесообразность проведения ремонта. Точные цены озвучиваются сразу после дефектовки на нашем предприятии, время дефектовки:
- гидроцилиндры — от 1 до 4 дней;
- гидромоторы/гидронасосы/распределители — от 3 до 7 дней;
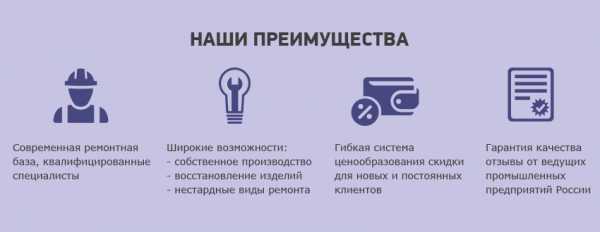
За более подробной информацией обращайтесь к нашим менеджерам по телефону: +7 (495) 660-04-23
РЕМОНТ И ОБСЛУЖИВАНИЕ
ЛЮБОЙ ГИДРАВЛИКИ
www.hydrott.ru
Ремонт Гидронасосов Разных Видов: Поэтапная Инструкция
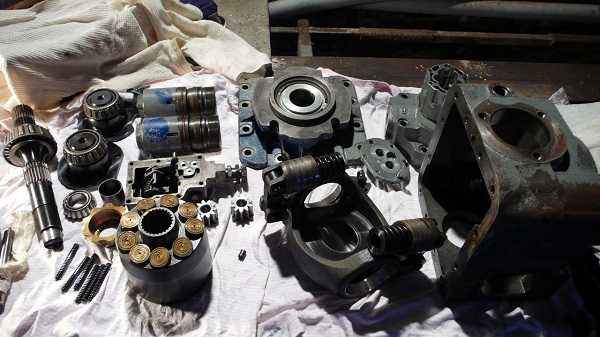
Ремонт гидронасоса
Ремонт гидравлических насосов часто необходим при возникновении проблем с такой специальной техникой. Часто, подобная ситуация не требует вмешательства квалифицированных специалистов и при наличии небольших определенных знаний можно своими руками ее исправить.
С наиболее распространенными неисправностями и способами их устранения предлагается познакомиться из статьи.
Разновидности и классификация гидронасосов
Работа любого гидронасоса основана на принципе всасывания и нагнетания жидкости.
Основные элементы конструкции:
- Камера всасывания.
- Камера нагнетания.
Между ними перемещается жидкость, которая при заполнении камеры нагнетания, начинает давить на поршень, вытесняя его, сообщая рабочему инструменту перемещение.
Основные рабочие параметры всех типов гидронасоса:
- Частота вращения вала двигателя, измеряется в об/мин.
- Рабочее давление в цилиндре, в Бар.
- Объем рабочей жидкости, в см³/об или количество жидкости, вытесняемое насосом за один оборот вала двигателя.
Основные разновидности оборудования:
- Ручной гидравлический гидронасос. Это простейший агрегат, работающий по принципу вытеснения жидкости.
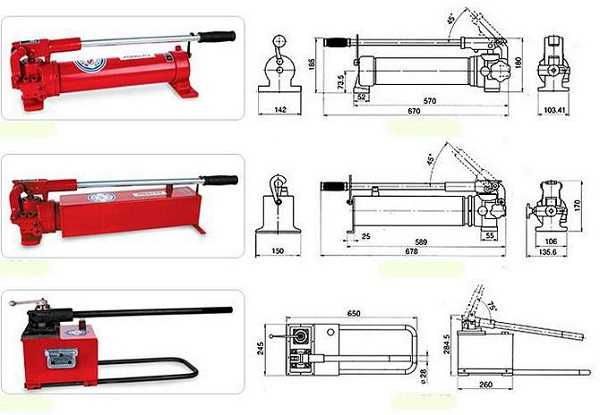
Ручной гидронасос
При нажатии ручки происходит перемещение поршня вверх, что создает силу всасывание и посредством клапана КО2 в камеру поступает жидкость, вытесняемая при поднятии рукояти.
Преимущества таких агрегатов:
- относительная простота конструкции, что облегчает ремонт при необходимости;
- надежность;
- низкая цена.
Недостаток:
- низкая производительность, по сравнению с приводными агрегатами.
- Радиально-поршневые. Способны развивать давление до 100 Бар, имеют длительный период работы. Радиально-поршневые насосы могут быть двух типов:
- роторными. В таких устройствах поршневая группа помещена внутри ротора, от его вращения поршень совершает возвратно-поступательные перемещения, поочередно стыкуясь с отверстиями для слива жидкости через золотники;
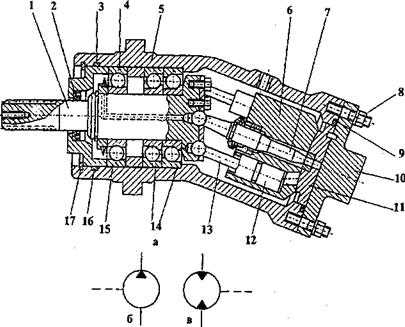
Устройство роторного радиально-поршневого насоса
- с эксцентричным валом. Его отличие — расположение поршневой группы внутри статора, такие насосы распределяют жидкость через клапана.
Преимущества оборудования:
- высокая надежность;
- работа выполняется с высоким давлением, что увеличивает производительность;
- при эксплуатации создает минимальный уровень шума.
Недостатки агрегата:
- при подаче жидкости высокий уровень пульсации:
- большая масса.
- Аксиально-поршневые. Это наиболее распространенный тип оборудования.
В зависимости от расположения оси вращения двигателя могут быть:
- наклонными;
- прямыми.
Преимущества таких насосов:
- большой КПД;
- высокая производительность.
Основной недостаток:
- высокая стоимость.
- Шестеренные насосы относятся к роторному оборудованию. Гидравлическая часть конструкции состоит из двух вращающихся шестерней, их зубья при контакте вытесняют из цилиндра жидкость. Шестеренчатые насосы могут быть:
- с внешним зацеплением;
- с внутренним зацеплением, при котором шестеренки расположены внутри корпуса.
На фото представлены типы шестеренных насосов.
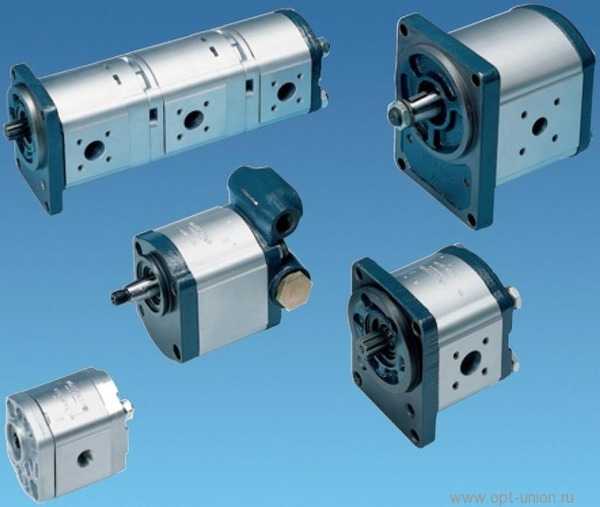
Шестеренные насосы
Шестеренные агрегаты используются в системах, где уровень рабочего давления не превышает 20 МПа. Они больше всего применяются в сельскохозяйственном и строительном оборудовании, системах подачи материалов для смазки узлов и мобильной гидравлике.
Устройства имеют:
- Простую конструкцию.
- Небольшие размеры.
- Малый вес.
Недостатки:
- Низкий КПД, до 85%.
- Небольшие обороты.
- Короткий эксплуатационный ресурс.
Основные неисправности гидронасосов и способы их устранения
Совет: Для увеличения срока службы гидронасоса необходимо строго соблюдать требования инструкции по эксплуатации.
Практически все поломки, возникающие при работе гидронасосов, являются следствием таких факторов, как:
- Несоблюдение правил управления оборудованием и пренебрежение при его техническом обслуживании:
- несвоевременной заменой масла и фильтров;
- устранением протечек в гидравлической системе.
- Ошибки при подборе гидравлической жидкости или масла.
- Использование комплектующих, которые не соответствуют режиму эксплуатации насоса.
- Неправильная настройка оборудования.
В таблице представлен список наиболее частых неисправностей и способы их устранения:
Поломка гидронасоса | Вероятная причина | Инструкция устранения неполадки |
Нестабильность при работе | Износилось или повредилось седло подшипника и поверхность люльки насоса. Зазор в тяге механизма управления. Поломались штифты седла подшипника. Загрязнился канал между золотником управления и поршнем. Задиры, полученные на поверхности поршня, препятствуют его плавному передвижению | Произвести внешний осмотр. Проверить и отремонтировать, при необходимости, гидронасос |
Задиры, возникшие на поверхности золотника управления, препятствуют плавному перемещению поршня | Познакомиться с соответствующим разделом в руководстве, выпускаемом службой контроля за гидравлическим оборудованием | |
Неисправные элементы компенсатора давления в контуре. Повысилось сопротивление гидравлической линии, расположенной между удаленными элементами компенсатора давления и пультом управления. Низкое давление управления | Проверить работу гидролинии Настроить давление управления оборудованием | |
Гидронасос выдает малый расход | Задиры или износ цилиндра и сопряженных поверхностей на тарелке клапана. Износились шлицы приводного вала. Износились или повредились башмаки поршней или сами поршни | Сравнить с соответствующими техническими характеристиками гидронасоса |
Износились поршневые отверстия блока цилиндров. Чрезмерно износились подшипники | Проверить работу гидронасоса и, при необходимости, отремонтировать | |
При низком давлении появляются вибрации | Неправильно настроен максимальный объем насоса | Выполнить регулировку максимального расхода |
Слишком приближено к рабочему давлению компенсаторное давление. Неправильно выставлен компенсатор давления. Сломался золотник механизма управления. Повредились или переломались пружины золотника управления. Образовались задиры на золотнике или в отверстии. Повредились или переломались пружины цилиндра управления. Неисправности элементов в контуре удаленного компенсатора давления | Познакомиться с соответствующим разделом в руководстве, выпускаемом службой контроля за гидравлическим оборудованием | |
Сильные перепады давления | Слишком высоко установлен компенсатор давления. Слишком большой выставлен минимальный рабочий объем оборудования. Износились или повредились опорные поверхности люльки гидронасоса и седла опорных подшипников | Познакомиться с соответствующим разделом в руководстве, выпускаемом службой контроля за гидравлическим оборудованием Проверить и если нужно отремонтировать гидронасос |
Загрязнился канал между поршнем управления и золотником, нарушилась пловность хода поршня. Загрязнился канал от выходного канала к золотнику управления | Проверить и отремонтировать гидронасос | |
Рабочее давление гидронасоса длительное время превышает номинальные или пиковые значения. В резервуаре низкий уровень рабочего состава. Низкое давление на входе в гидронасос. | Проверить уровень жидкости в емкости выше линии всасывания | |
Воздух попал в гидросистему | Ликвидировать негерметичность соединений, позволяющих воздуху проникать в жидкость | |
Насос сильно нагревается | Износились опоры поршней и блока цилиндров. Износились или повредились поверхности сопряжения между блоком цилиндров и распределителем. | Проверить и при необходимости выполнить ремонт насоса гидравлического. |
Неисправность компонента схемы: предохранительный клапан работает непрерывно или допускаются утечки жидкости под высоким давлением. Плохое охлаждение теплообменника. Необходимо осмотреть теплообменник, промыть и очистить охлаждающие поверхности. Объем бака недостаточный | Ликвидировать утечки или заменить неисправные детали | |
Насос неправильно работает под нагрузкой или остановился | Убедиться в правильности управления | |
В резервуаре низкий уровень жидкости | Проверить уровень жидкости в емкости | |
Гидронасос издает чрезмерный шум | Появился воздух при всасывании. Износилась роторная группа насоса | Ликвидировать негерметичность всасывающего трубопровода. Заменить блок цилиндров, опорные подшипники, прижимные пластины, поршни, люльку. Выполнить ремонт гидравлического насоса |
Слишком большая вязкость жидкости | Выбрать правильно вязкость рабочей жидкости | |
Входной вал насоса вращается неправильно, в другом направлении | Проконтролировать и исправить, при необходимости, направление вращения вала. |
Мелкий ремонт насосов гидравлических не является серьезной проблемой, при наличии под рукой ремкомплекта.
Обычно в него входят:
- Запасные фильтры.
- Резинотехнические элементы.
- Уплотнительные втулки.
Совет: Приобретая гидронасос, необходимо проверить наличие всех комплектующих и инструкции по эксплуатации оборудования.
Как правильно выполнить ремонт насосов гидросистемы, более подробно подскажет видео в этой статье.
moikolodets.ru
Ремонт гидравлической аппаратуры
Надежность работы, чувствительность и точность регулирования гидравлической аппаратуры зависят от величины зазоров и состояния поверхностей в подвижных соединениях.
В процессе эксплуатации вследствие износа рабочих элементов зазоры в гидравлических аппаратах увеличиваются, а качество рабочих поверхностей ухудшается. Ухудшается геометрическая точность элементов гидроаппаратуры. В таблице 1 приведены ориентировочные величины рабочих зазоров между плунжерами и корпусами гидроаппаратов, а на рисунке 2 — средний срок их службы.
Ремонт деталей
Корпусы
Ремонт корпусов гидравлической аппаратуры заключается в восстановлении геометрической точности отверстий иод плунжеры, улучшении качества рабочих поверхностей (удалении рисок и задиров, уменьшении шероховатости). Отверстия развертывают и доводят притиркой. Допуск на доводку должен быть 0,05 мм. При износах свыше 0,2—0,3 мм отверстия растачивают или шлифуют. При обработке отверстий ступенчатой формы для обеспечения соосности вначале обрабатывают отверстие, имеющее наибольшую длину, а затем по первому обработанному отверстию обрабатывают второе. Направление инструмента осуществляют с помощью стальной втулки, которую устанавливают на цилиндрический хвостовик инструмента.
Рабочие зазоры гидроаппаратов
Наименование гидроаппарата | Диаметр плунжера. мм | Рабочий зазор, мы |
Гидрораспределители управления | До 10 | 0,008-0,01 |
10-20 | 0,01-0,02 | |
Св. 20 | 0,02-0,03 | |
Гидрораспределители: | ||
силовых головок агрегатных станков; | — | 0,01-0,015 |
гидропанелей шлифовальных, долбежных и строгальных станков; | — | 0,015-0,025 |
стандартной распределительной гидроаппаратуры, выпускаемой отдельными узлами | — | 0,02—0,03 |
Напорные и переливные гидроклапаны | До 20 | 0,015-0,02 |
20-30 | 0,02-0,035 | |
Регуляторы потока: | ||
силовых головок агрегатных станков | До 12 | 0,002-0,005 |
Св. 12 | 0,015-0,02 | |
стандартных узлов и стандартных редукционных клапанов | До 12 | 0,010—0,015 |
Св. 12 | 0,035-0,05 | |
Напорные гидроклапаны сливных гидролиний | — | 0,015-0,02 |
Гидродроссели | До 16 | 0.015-0.02 |
Св. 16 | 0,02-0,025 | |
Крановые гидроаппараты | До 20 | 0.02-0.025 |
Св. 20 | 0,02-0,035 |
Шероховатость рабочих поверхностей после развертывания или шлифования не должна быть более Ra = 1,25 —0,63 мкм, после доводки — не более 0,63—0,32 мкм.
Новые корпусы изготовляют из чугуна СЧ 21-40. После механической обработки на рабочих поверхностях не должно быть раковин, пористости и посторонних включении. На нерабочих поверхностях допускаются отдельные рассредоточенные раковины не более 1/4 толщины стенки и диаметром не более 2 мм, но они должны быть залиты полимерным материалом, например клеем на основе эпоксидной смолы ЭД6. Корпус должен быть проверен на герметичность при давлении, в 1,5 раза превышающем максимальное рабочее давление, при этом внешние утечки и «отпотевание» поверхности корпуса не допускаются. Корпусы перед сборкой должны быть тщательно промыты.
Плунжеры
При восстановлении отверстии в корпусах плунжеры заменяют новыми. Наиболее распространенный материал для изготовления плунжеров—цементируемые стали 20, 20Х, а также стали марок 40Х, ХВГ, ШX15. Сортамент заготовки — прокат, исправление правкой не допускается.
Средний срок службы гидрооборудованияПосле черновой токарной обработки с припуском 0,4—0,6 мм плунжеры термически обрабатывают до твердости HRC 50—54. После шлифования торцов и зачистки фасок плунжеры шлифуют по наружному диаметру на бесцентрово-шлифовальном станке. После шлифования плунжер должен иметь размер меньше фактического размера восстановленного отверстия корпуса на половину величины допускаемого зазора (см. рис. 1). После шлифования плунжер прирабатывают по месту без смазки, обеспечивая легкость, хода. При изготовлении плунжеров необходимо соблюдать следующие технические требования:
- конусность и овальность рабочих диаметров должна составлять 0,002—0,005 мм, огранка—не более 0,005 мм;
- несоосность шеек одного диаметра не допускается, несоосность шеек различных диаметров не должна превышать величину наименьшего зазора между отверстиями и шейками; биение рабочих поверхностей относительно нерабочих — не более 0,05 мм;
- шероховатость рабочих поверхностей Ra = 0,32 мкм не более.
Клапаны
Шариковые и конические клапаны в связи с ударным характером работы значительно подвержены износу. Ремонт этих клапанов заключается в замене изношенных шариков, конусов и седел с последующей подгонкой деталей по месту. Седла шариковых клапанов изготовляют из сталей марок 45, 40Х, 45Х с термической обработкой до твердости HRC 35—40. Для обеспечения герметичности конические клапаны и седла изготовляют из материалов различной твердости: сталь закаленная (HRC 45—48) — сталь незакаленная, сталь закаленная — чугун, сталь закаленная — бронза. Из менее твердых материалов обычно изготовляют седла. При замене седел, изготовленных из мягкого материала, подгонка (притирка) клапана может быть заменена опрессовкой (вдавливанием клапана под прессом).
Детали клапанов золотникового типа восстанавливают теми же способами, какими восстанавливают корпуса и плунжеры.
Пружины
Пружины в процессе эксплуатации получают усталостную осадку, что приводит к изменению их характеристик. Пружины, получившие значительную осадку, рекомендуется заменять новыми. При ремонте гидроаппаратуры пружины изготовляют из пружинной проволоки I и II класса по ГОСТ 9389—60 холодной навивкой на токарных станках с помощью оправок. Шаг пружины устанавливают соответствующей продольной подачей суппорта. Диаметр оправки
где dв — внутренний диаметр пружины, который необходимо получить; К — коэффициент, зависящий от характеристики материала проволоки (σв):
После навивки пружины подвергают низкому отпуску с температурой нагрева 200—350° С. Пружины из углеродистых и легированных сталей закаливают и отпускают. Для обеспечения стабильной работы пружины сжатия заневоливают — сжимают в оправках до соприкосновения витков и выдерживают в этом положении 24—48 ч; при этом в материале пружин создаются напряжения противоположного знака по отношению к напряжениям от внешних нагрузок.
Крайние витки пружин должны быть поджаты. Торцовые поверхности обрабатывают на заточных или плоскошлифовальных станках. Готовые пружины оксидируют или цинкуют.
Ремонт гидравлических следящих систем
Ремонт гидравлических следящих систем наиболее сложен, что объясняется необходимостью обеспечения высокой точности сопряжении и минимальных рабочих зазоров в гидроаппаратах при максимальной легкости перемещения подвижных органов. В гидравлических следящих системах наиболее быстро изнашиваются следящие устройства. Рассмотрим, например, конструкцию дросселирующего гидрораспределителя токарно-копировального полуавтомата мод. 1722 (рис. 3). В корпусе 1 запрессованы стальные закаленные кольца 2, в отверстиях которых помещен с диаметральным зазором 0,005 — 0,008 мм плунжер 3 гидрораспределителя. На плунжер действует пружина 4. С плунжером связан щуп 5, рабочий объем гидрораспределителя со стороны щупа герметизирован диафрагмой 6.
При эксплуатации гидрораспределителя изнашиваются кольца и плунжер. Правильная геометрическая форма деталей искажается (появляется овальность к конусность), увеличивается шероховатость рабочих поверхностей, рабочие кромки колец и торцов плунжера закругляются. Все это приводит к ухудшению чувствительности следящего устройства.
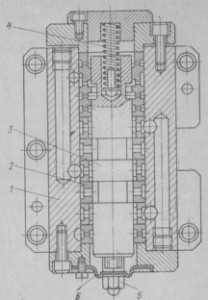
Для устранения износа колец, не выпрессовывая из корпуса, их . притирают, устраняя дефекты.
Шероховатость рабочих поверхностен должна быть Ra — 0,16 — — 0,080 мкм, овальность и конусность отверстия иод плунжер не более 0,002 мм, завал краев и острых кромок не допускается. При значительном износе кольца его заменяют.
Кольца изготовляют из стали ХВГ. После токарной операции и сверления отверстий кольца его термически обрабатывают до твердости HRC 62—65 с последующим искусственным старением. После старения кольцо сначала шлифуют по внутренней поверхности, а затем на оправке один из его торцов с последующей доводкой до биения не более 0,002 мм. На плоскошлифовальном станке шлифуют второй торец, оставляя припуск на последующую доводку 0,015 — 0,02 мм. Биение второго торца также должно быть не более 0,002 мм. Шероховатость поверхностей Rа = 0,016 — 0,80 мкм, завал торцов и закругление острых кромок не допускается.
Комплект колец шлифуют на оправке по наружной поверхности, обеспечивая натяг в сопряжении с притертым отверстием корпуса 0,005—0,01 мм. Затем кольца тщательно промывают, не снимая с оправки, и запрессовывают в корпус, предварительно нагретый до температуры 200° С. Для обеспечения равномерного прогрева корпуса и исключения деформаций нагрев осуществляют в масляной ванне со скоростью около 5° С в минуту. После запрессовки колец отверстие под плунжер притирают.
При замене колец в корпусе распределителя на новые размер их отверстия иод плунжер может быть несколько занижен с учетом восстановления изношенного плунжера. В таком случае тонким шлифованием подгоняют исправленный плунжер по окончательно притертому отверстию колец, обеспечивая зазор 0,005—0,008 мм.
При восстановлении отверстий колец плунжер необходимо заменить новым. Новые плунжеры изготовляют из стали ХВГ. После черновой обработки плунжер термически обрабатывают до твердости HRC 62—65 с последующим искусственным старением. После шлифования пазов окончательно шлифуют наружные поверхности плунжера, подгоняя его но восстановленным отверстиям колец и обеспечивая необходимые шероховатость и диаметральный зазор.
Также Вам будет интересно:
Загрузка…chiefengineer.ru